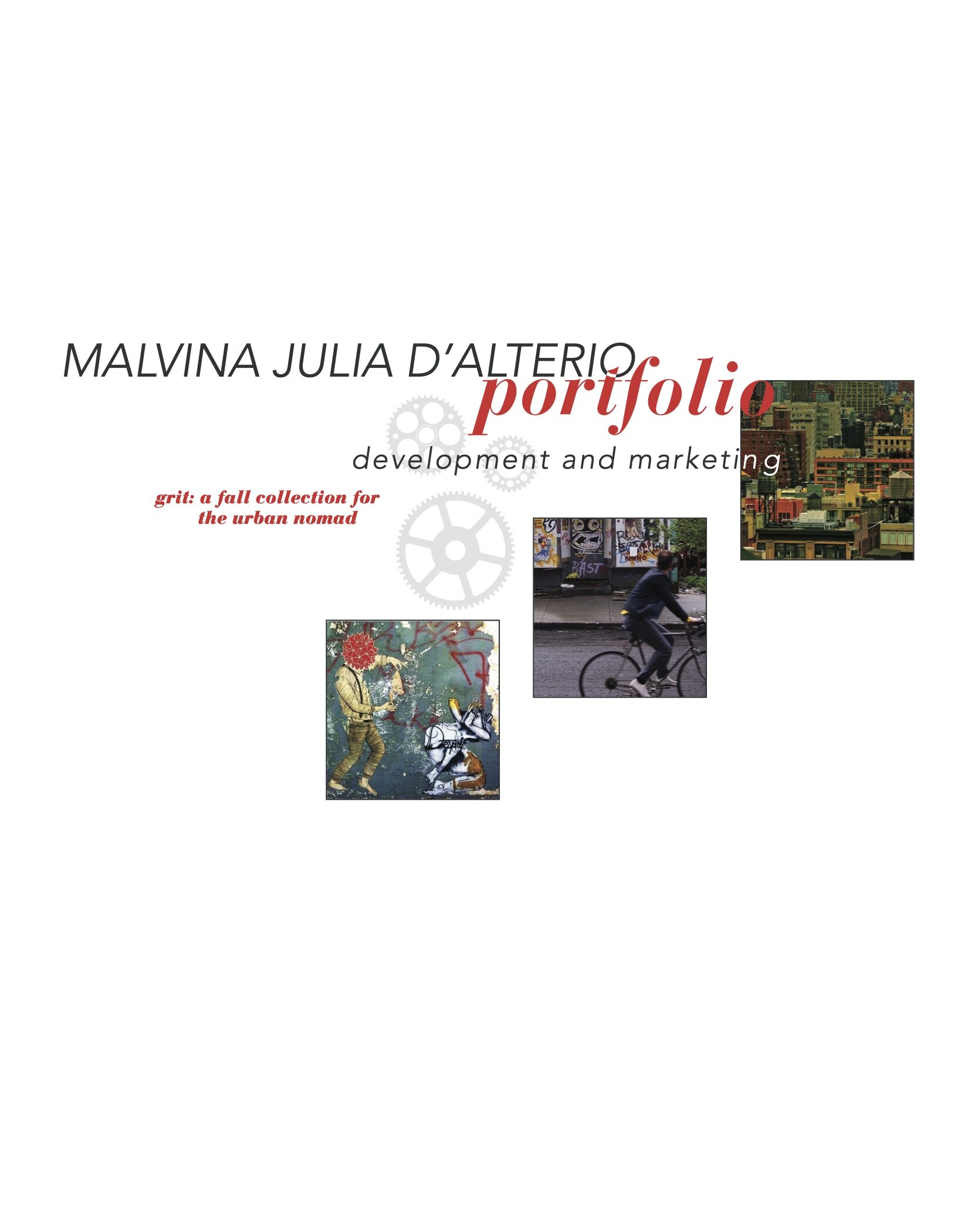
Developed between 2011 - 2014, This is a portfolio of work demonstrating experience developing textiles using both industrial and hand knitting and weaving techniques. The portfolio also includes a capstone project and examples of work done color matching dye and costing fabric for production.
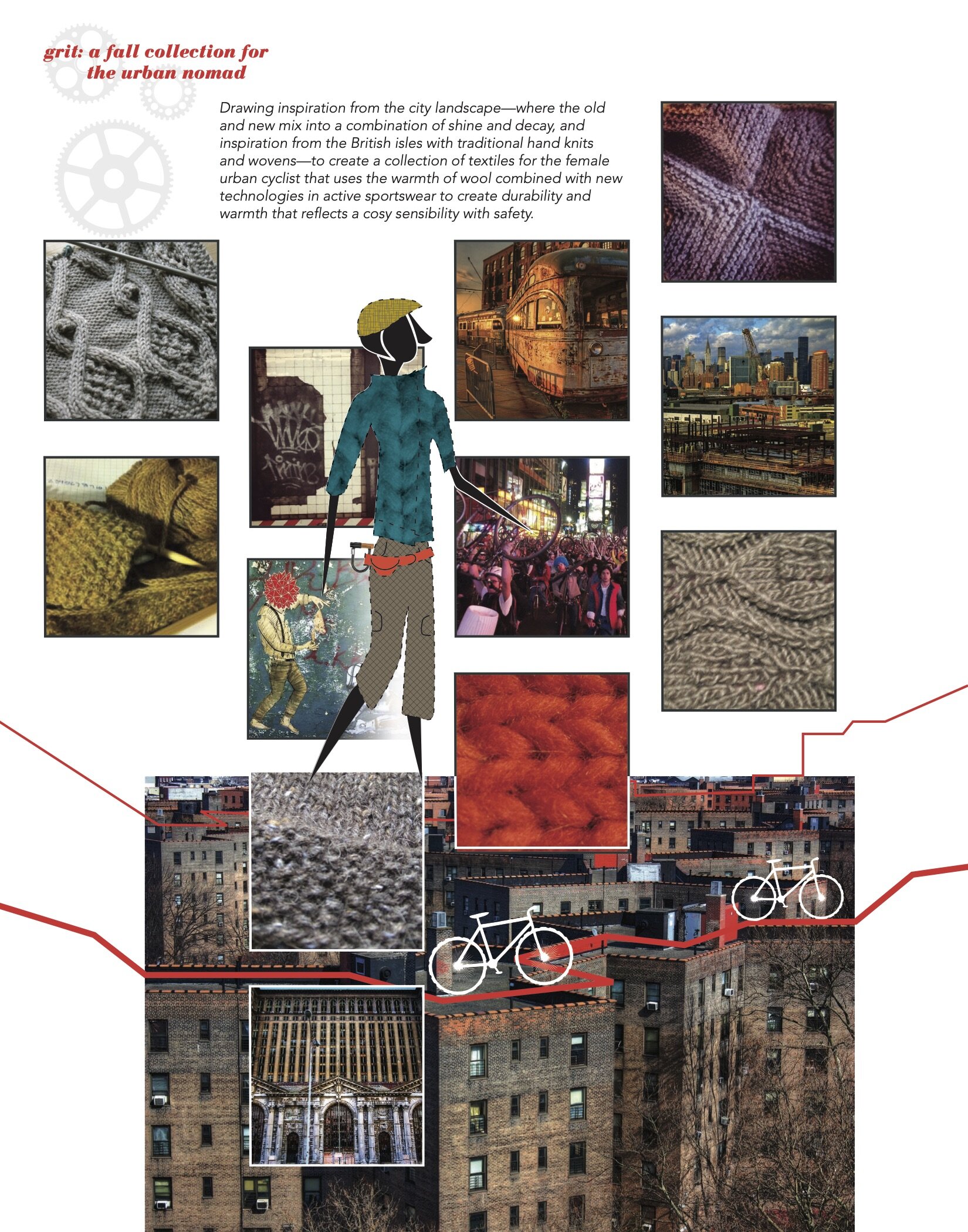
A mood board sets the tone of a project— colors, textures, inspiration, and includes language that briefly explains the project as a whole.
Notes: I fully acknowledge that I used some silly “hipster” terminology for thematic consistency.
Photography Myself or Lucas Cometto (by permission). Locations: Manhattan, Brooklyn, Queens, NY. Detroit, Michigan.
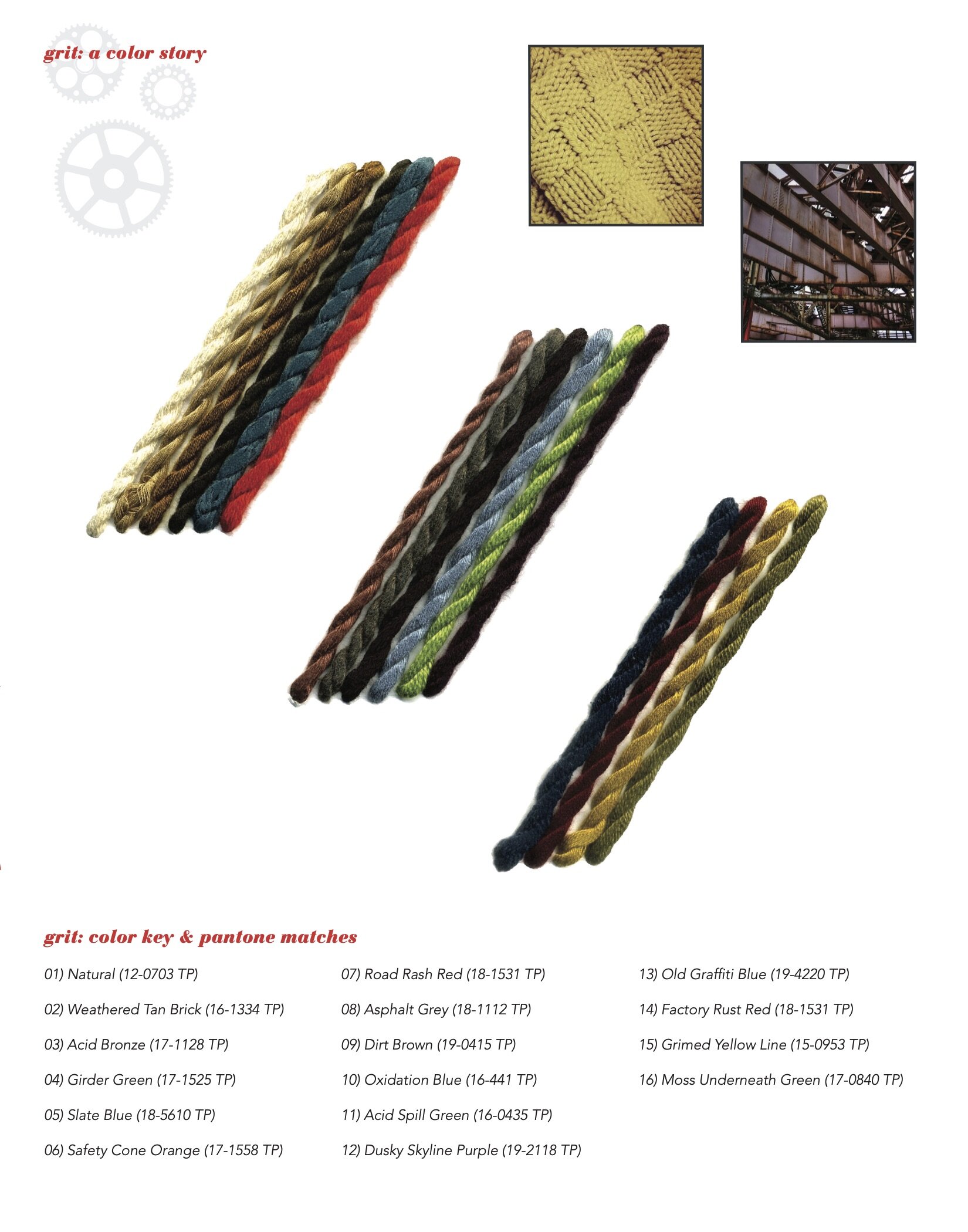
With a mood board, comes a color story.
The portfolio was originally a physical piece of work. Here you can see sets of colored thread, twisted into yarn hanks.
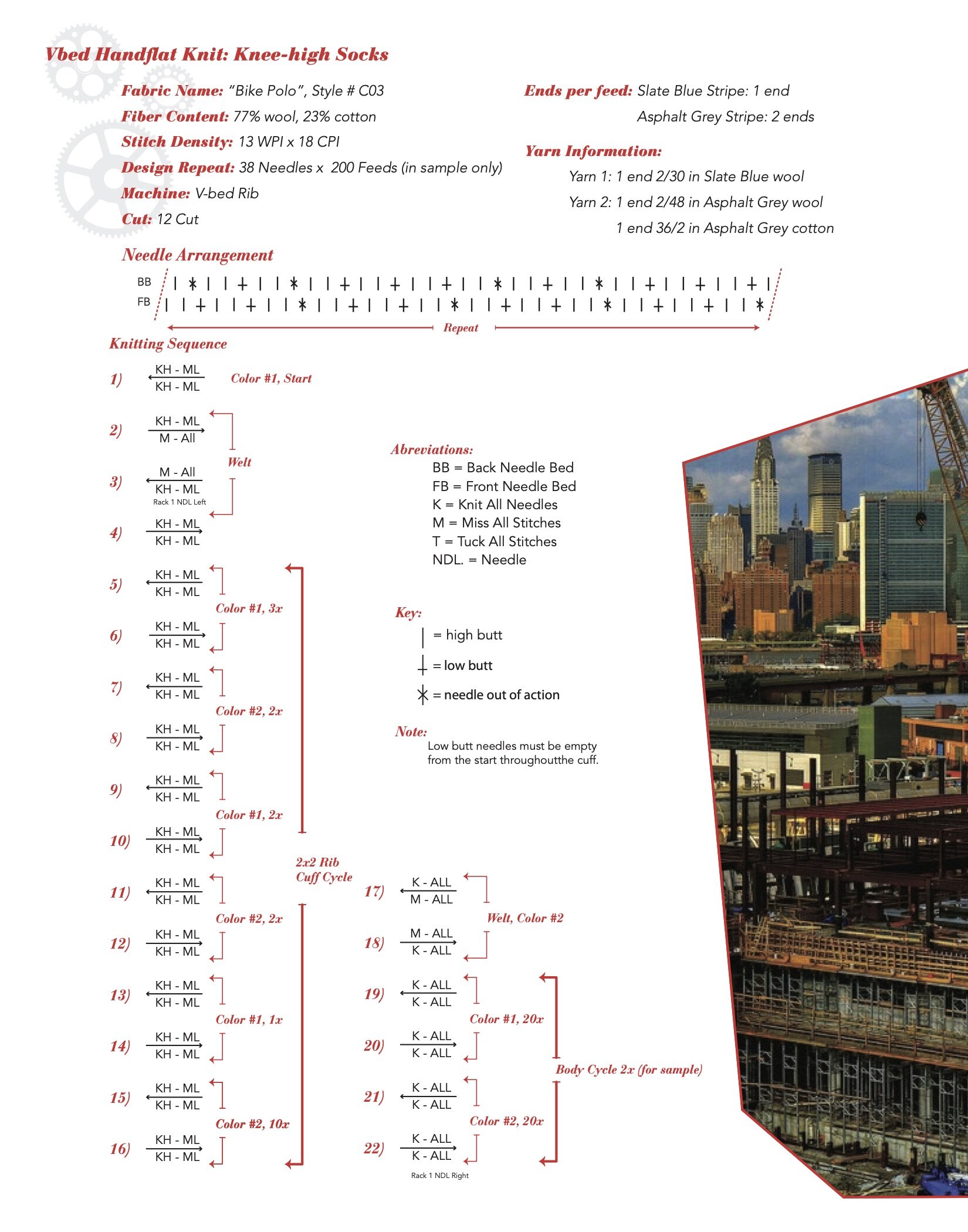
Diagrams and instructions for a Dubied Hand Flat knitting machine. Dubieds are in the shape of an inverted V, allowing for a variety of ribbed and lace-like patterning.

Knitted sample using a v-bed knitting machine, along with the color repeat diagram.
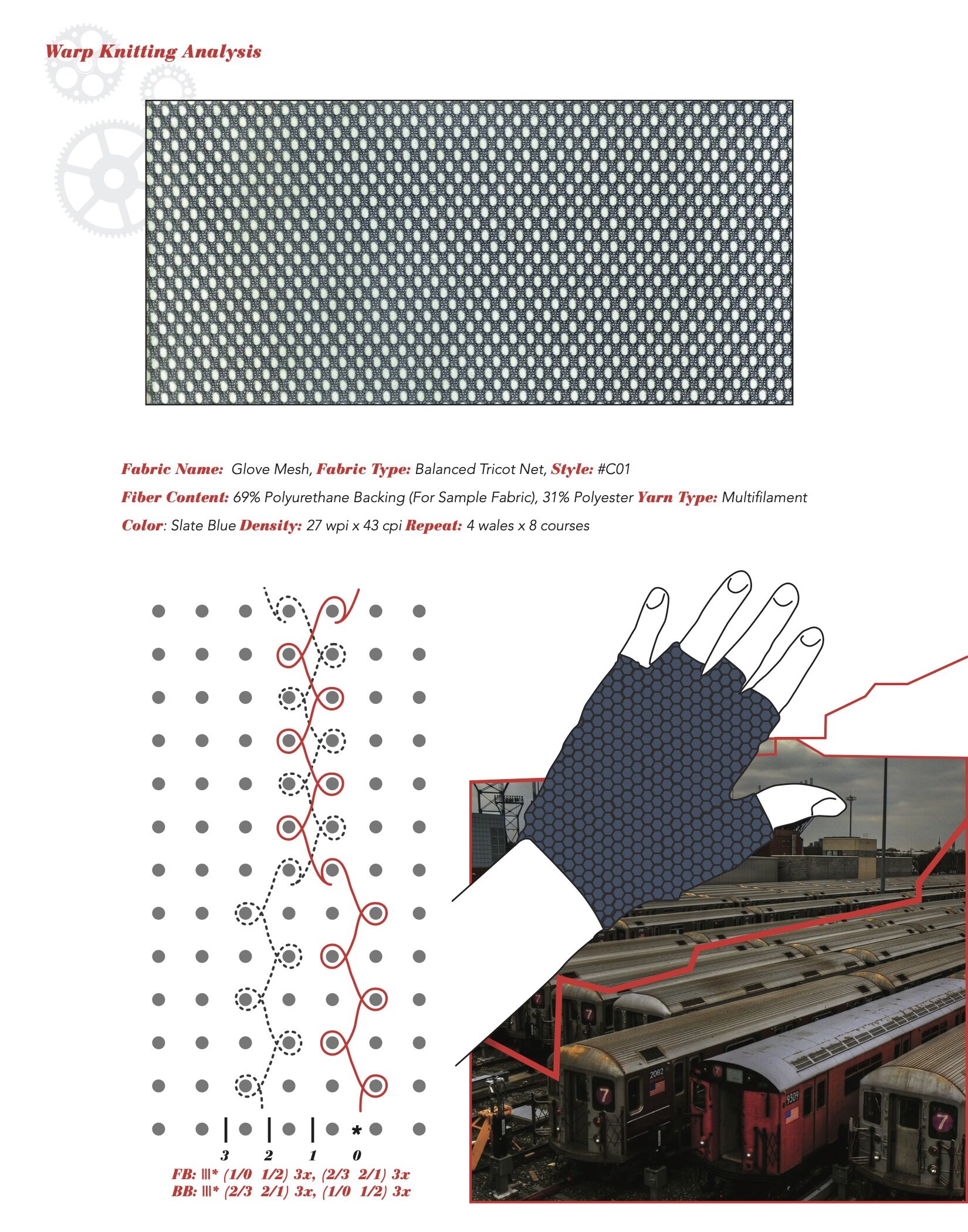
Analysis only, using a standard microscope. Warp knitting machines were not available on the FIT campus for use or demonstration. Warp knitting machines produce generally rigid fabrics, unlike weft knits. These machines are used to make various kinds of mesh and lace-like materials.
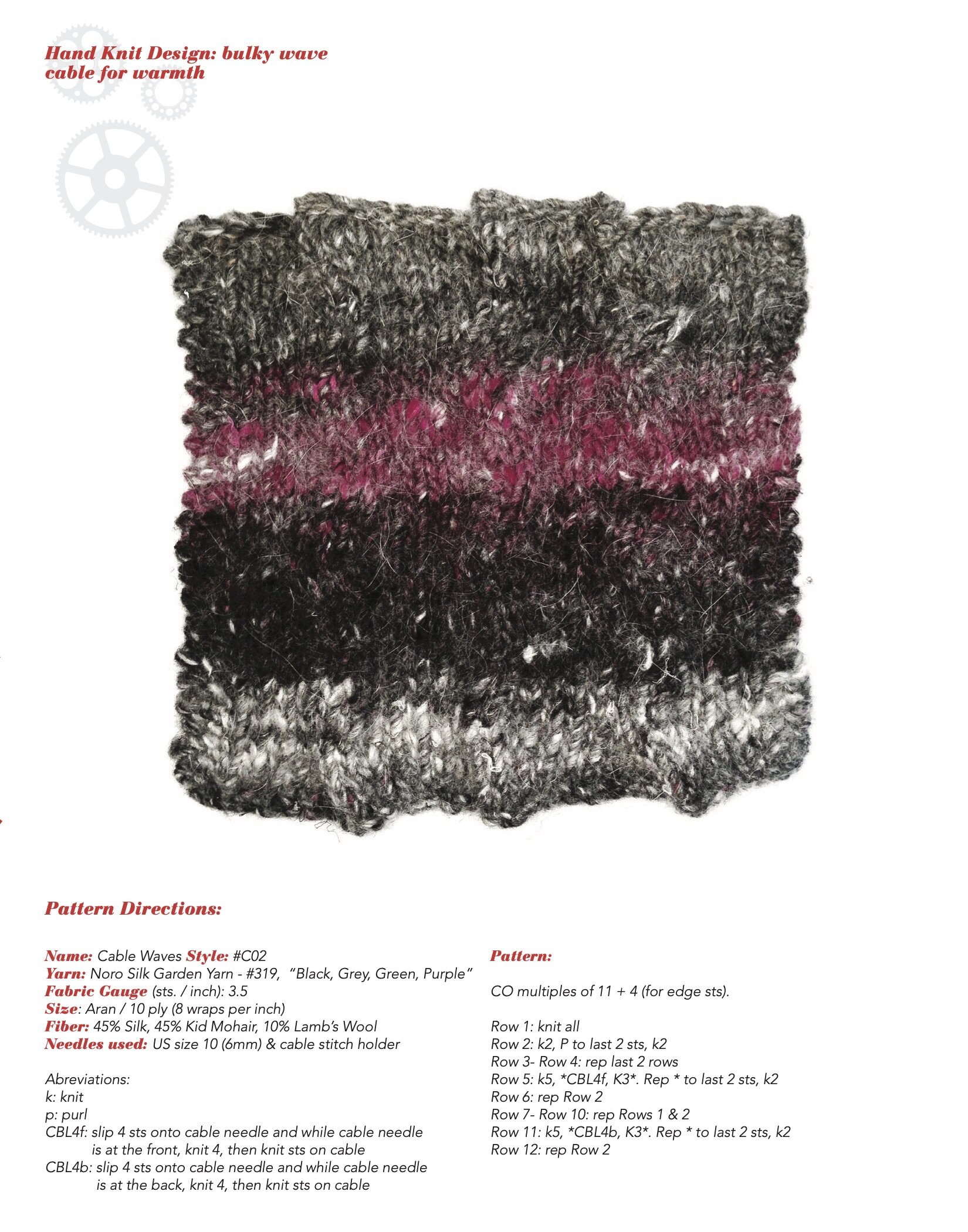
This pattern uses cabling techniques without using purl stitches for definition in order to create a wave-like landscape that creates air pockets for additional warmth.
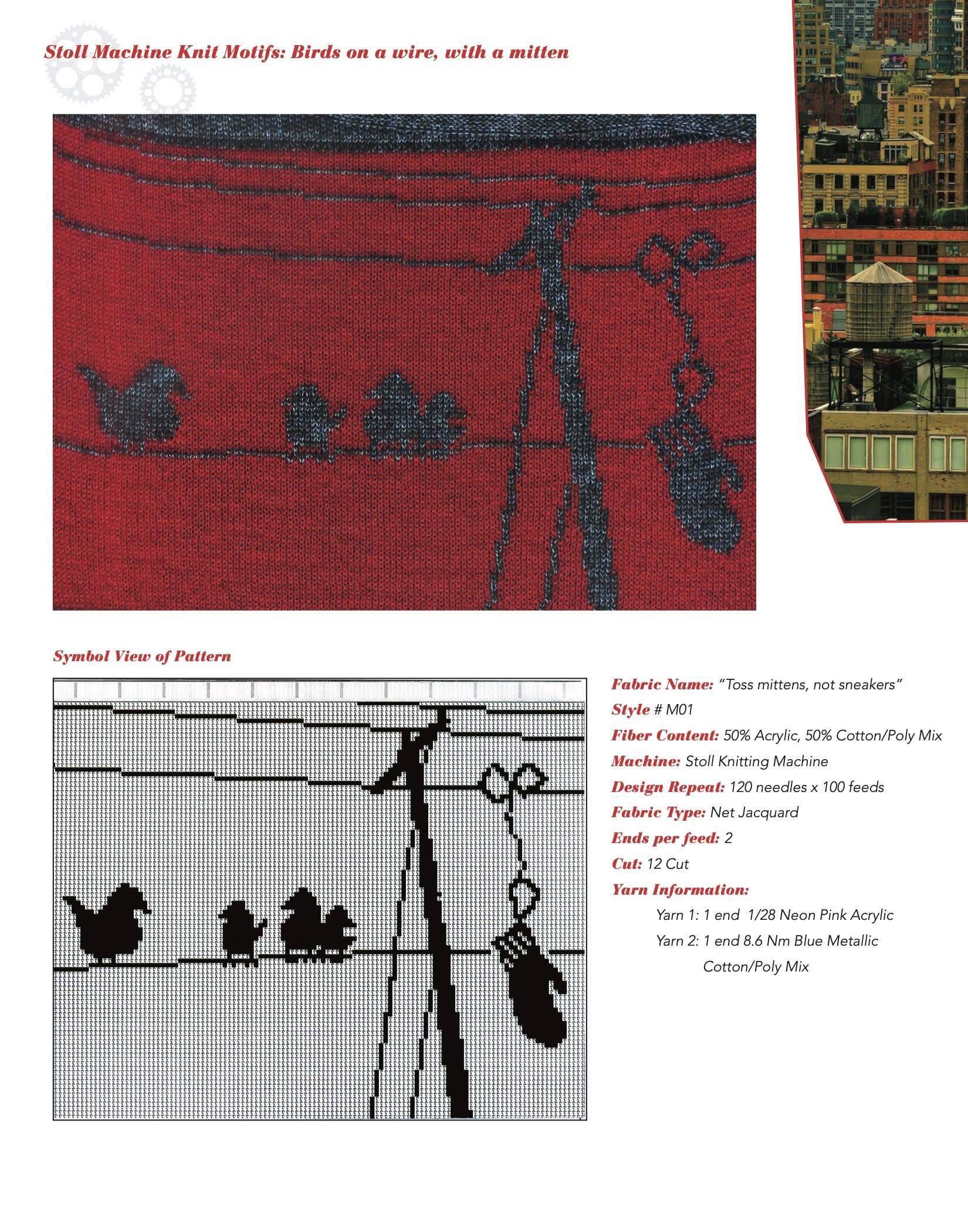
A net jacquard technique using a computer-programmable knitting machine. Software used is called Stoll M1 Plus.
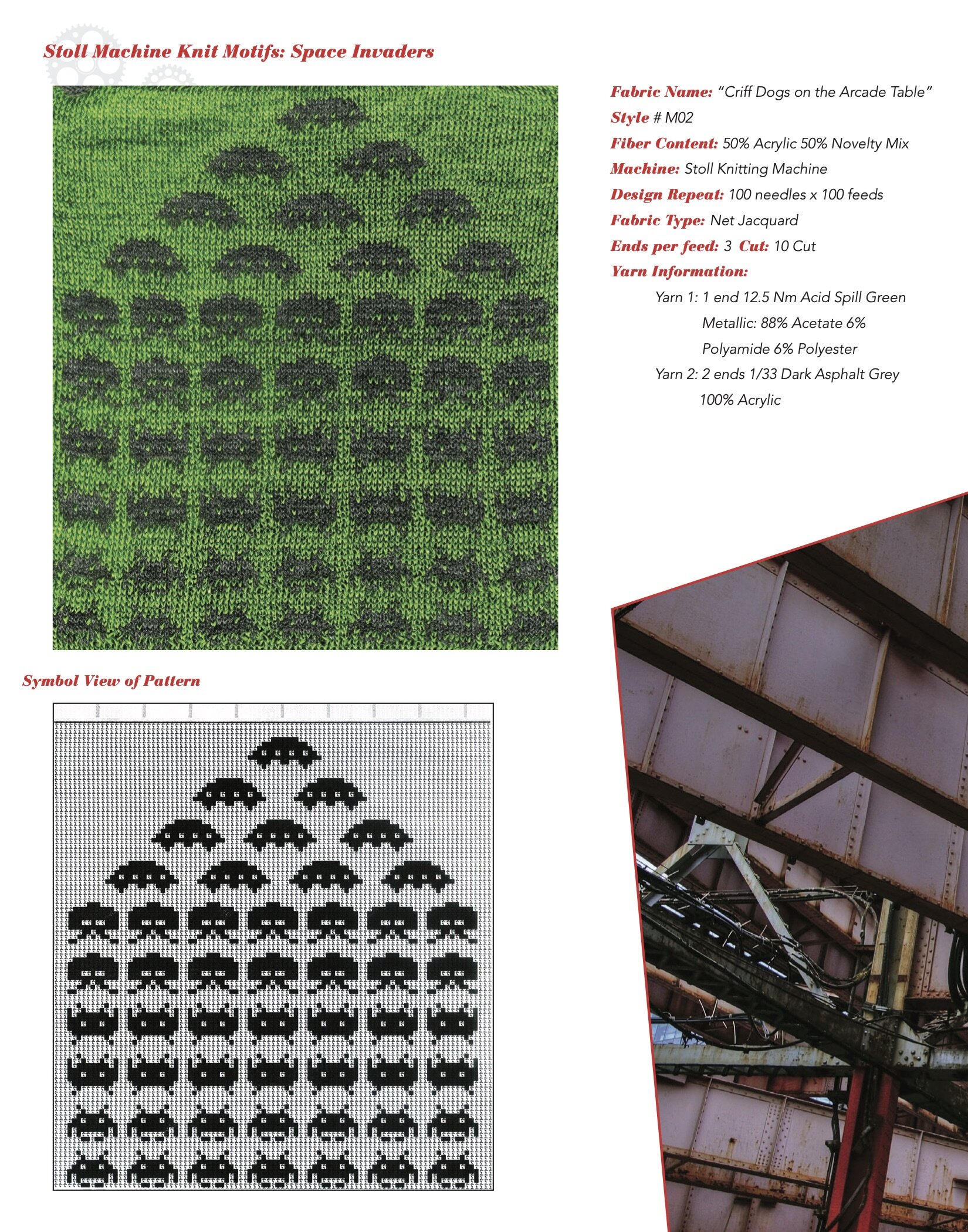
Similar to the first sample in technique, with an oldy but goody pattern.
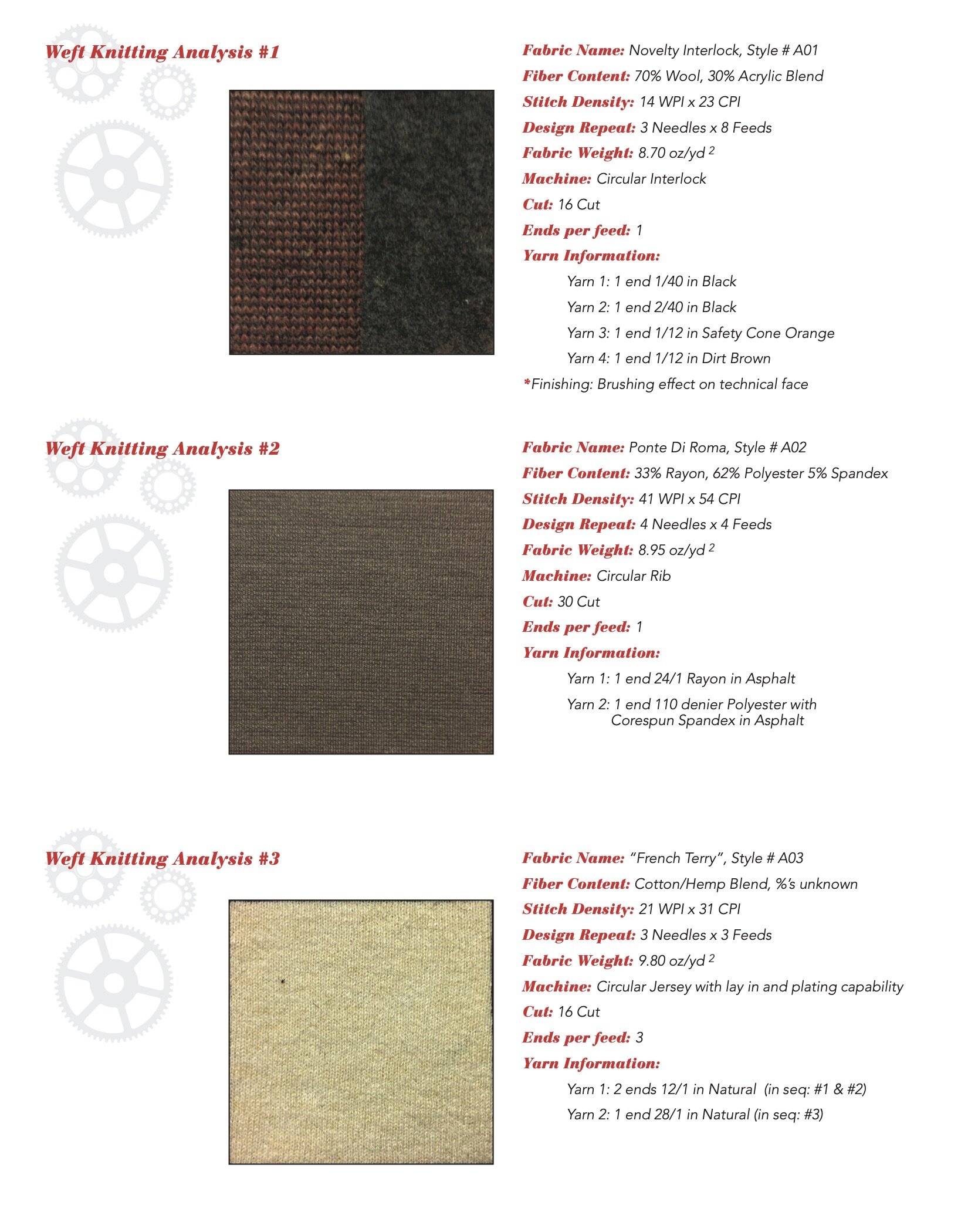
Weft knitting, or what most people think of as “knitting” is knitting done by hand or machine. All 3 samples are machine-knit. Most (but not all) cut and sew knit garments are made using some kind of circular knitting machine.
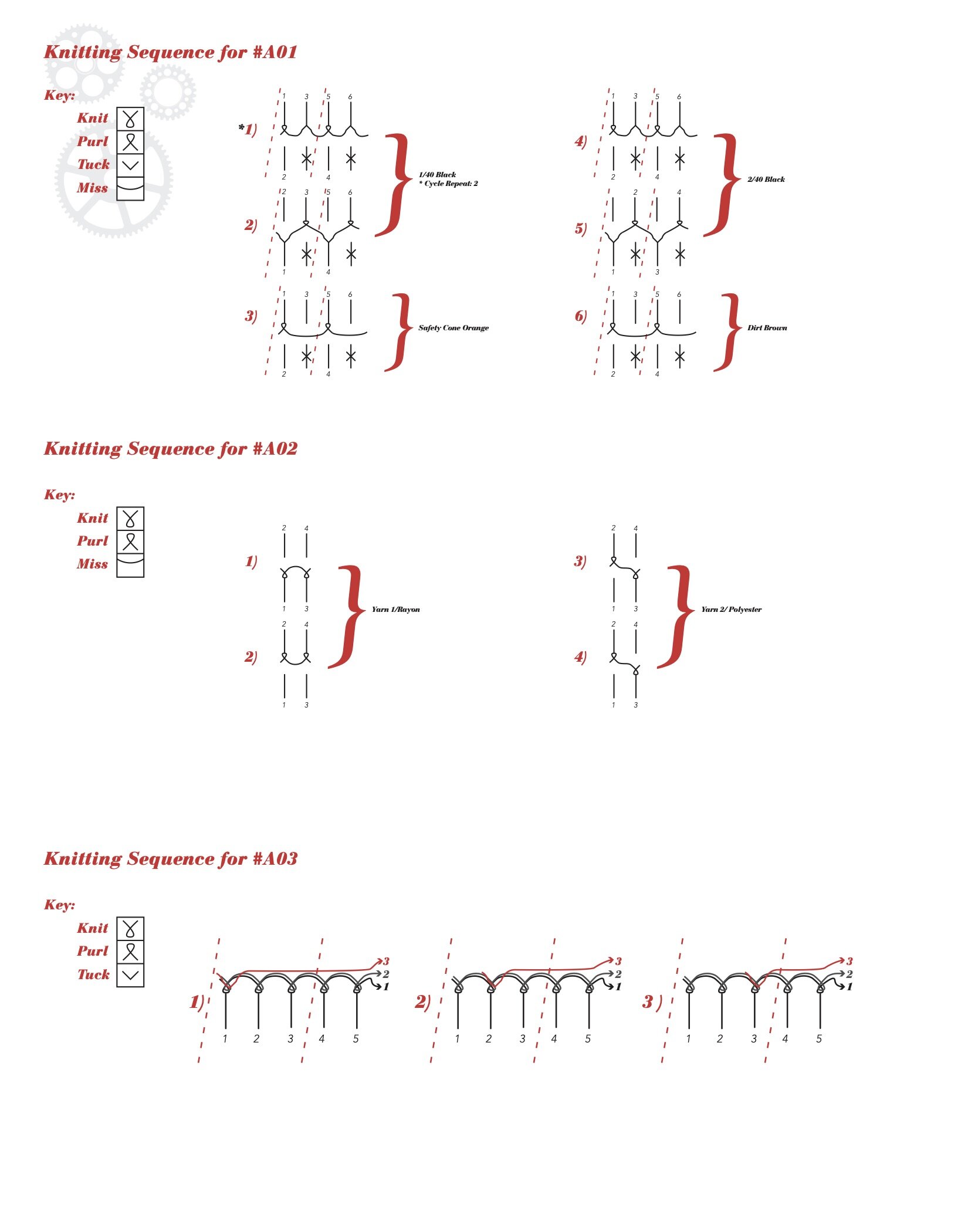
Pattern analysis for weft knits using loop diagrams.
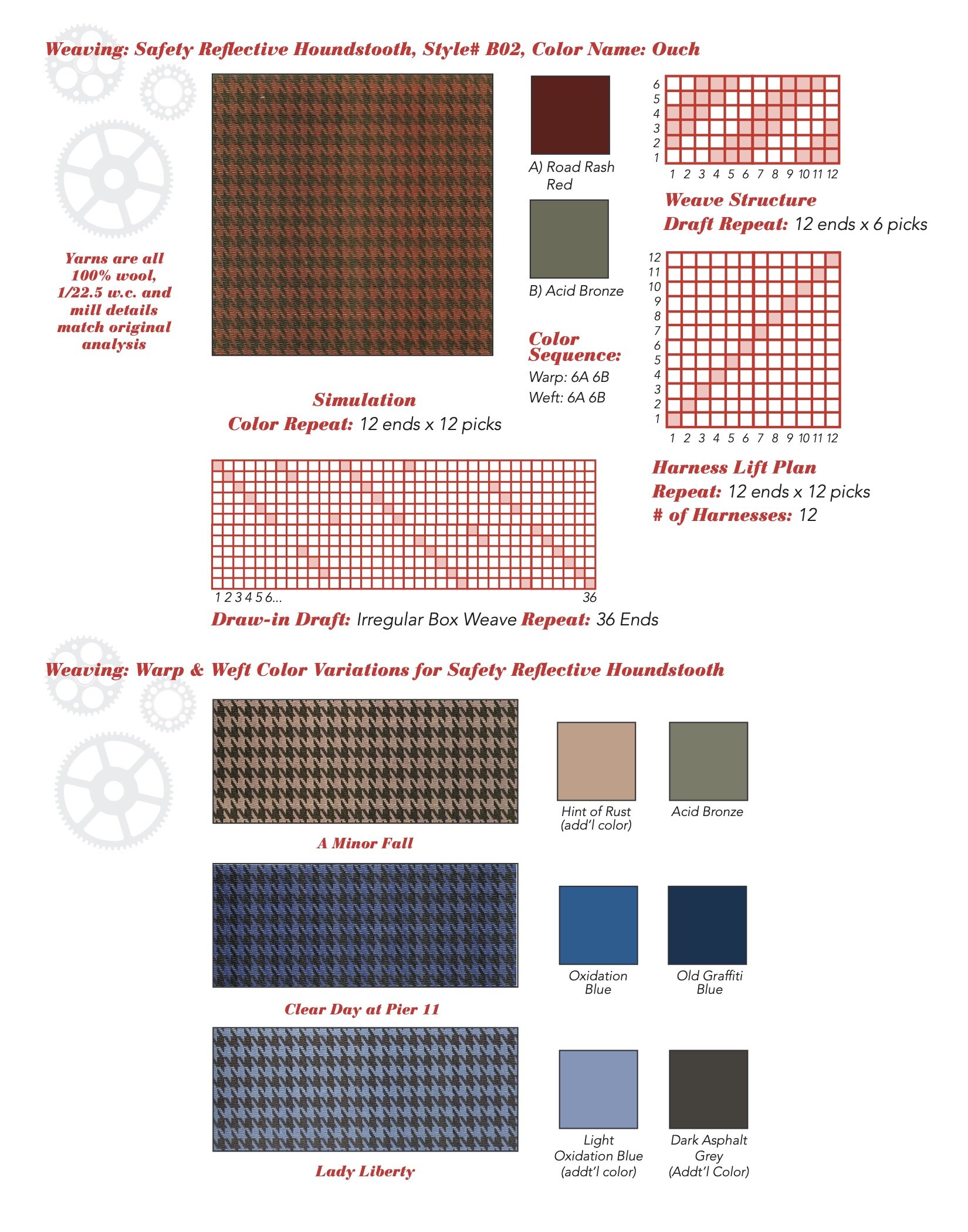
This shows the full setup for weaving a houndstooth fabric on a loom. Software used to develop rendering was Easy Weave and Dobby Pro.
Note: There is no need to make a houndstooth this difficult. It can be done on a 4 harness loom. It was only done this way to accommodate the next woven pattern.
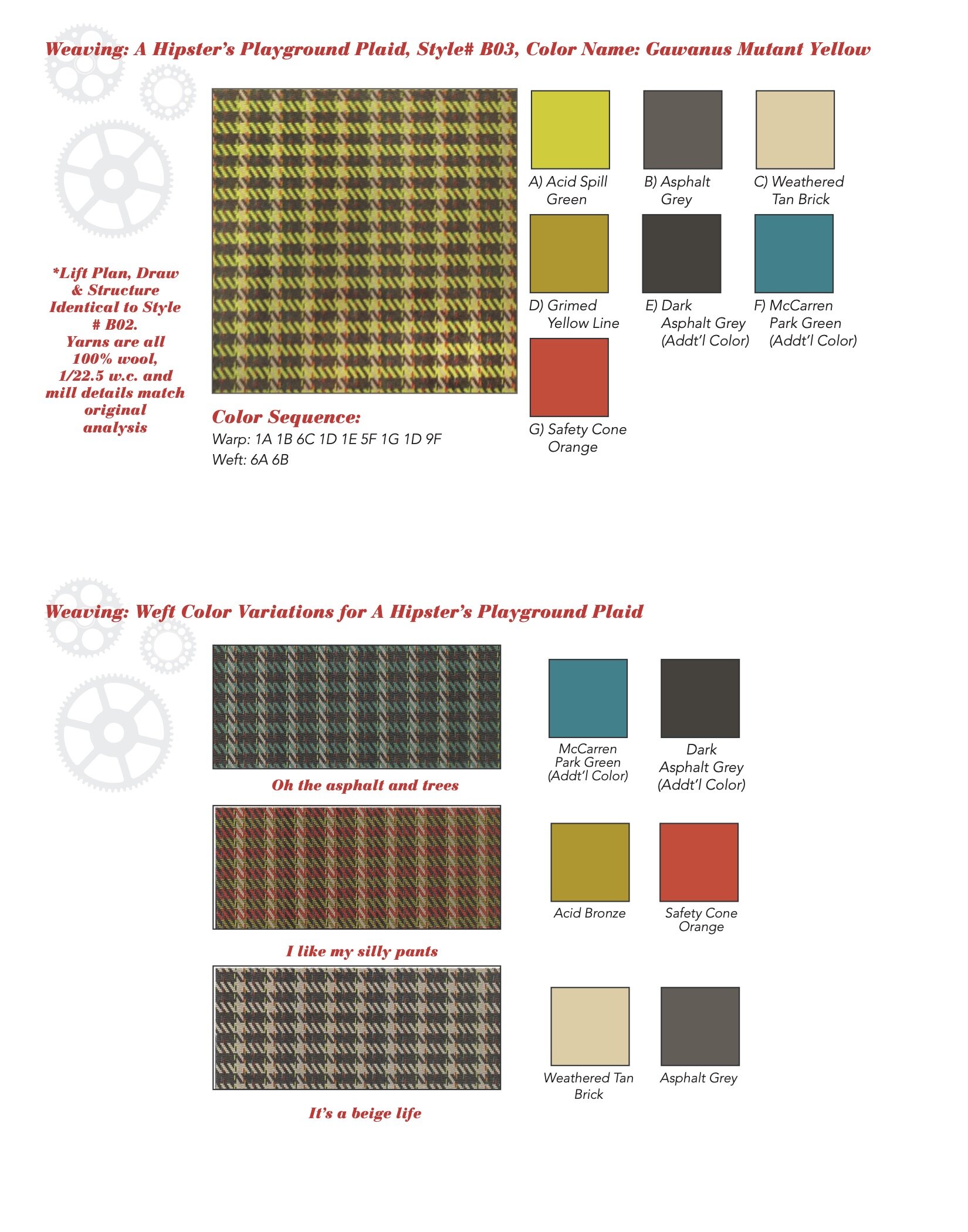
I’m pretty sure this pattern was developed first before the houndstooth, and then the houndstooth had to adapt to the number of harnesses required to make this work.
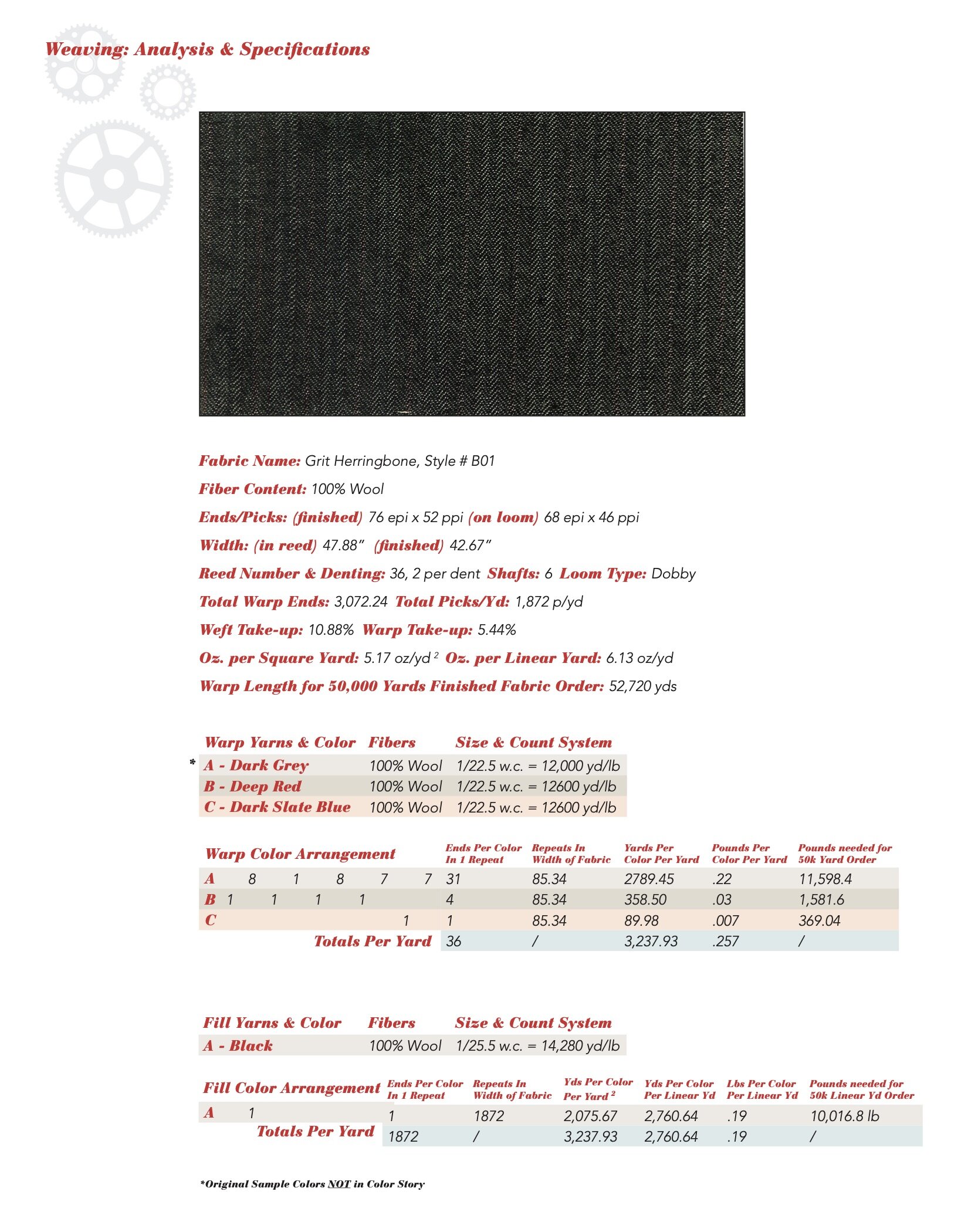
This includes a complete breakdown of an analysis done on a found piece of fabric, including what would be needed to reproduce it on an industrial loom.
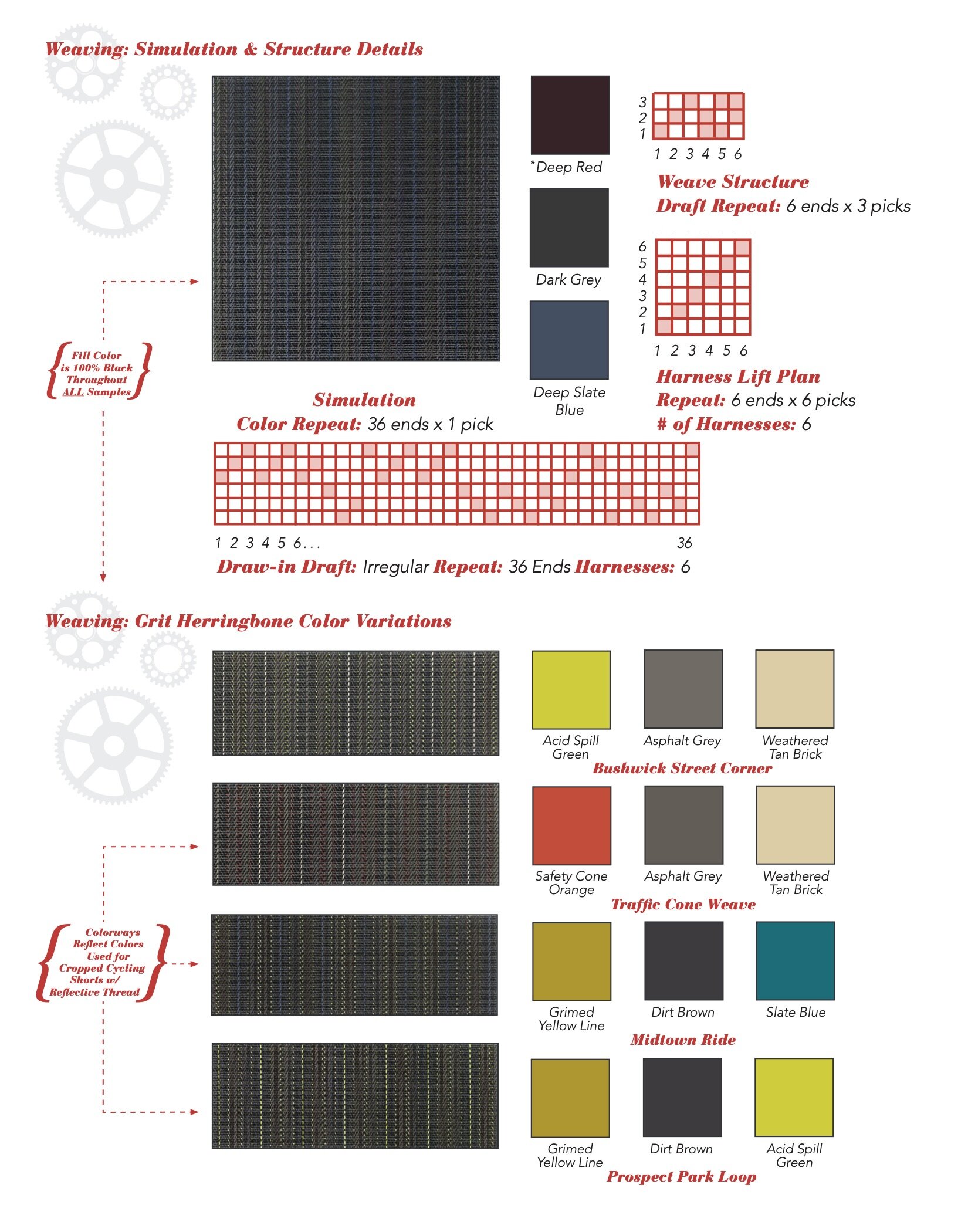
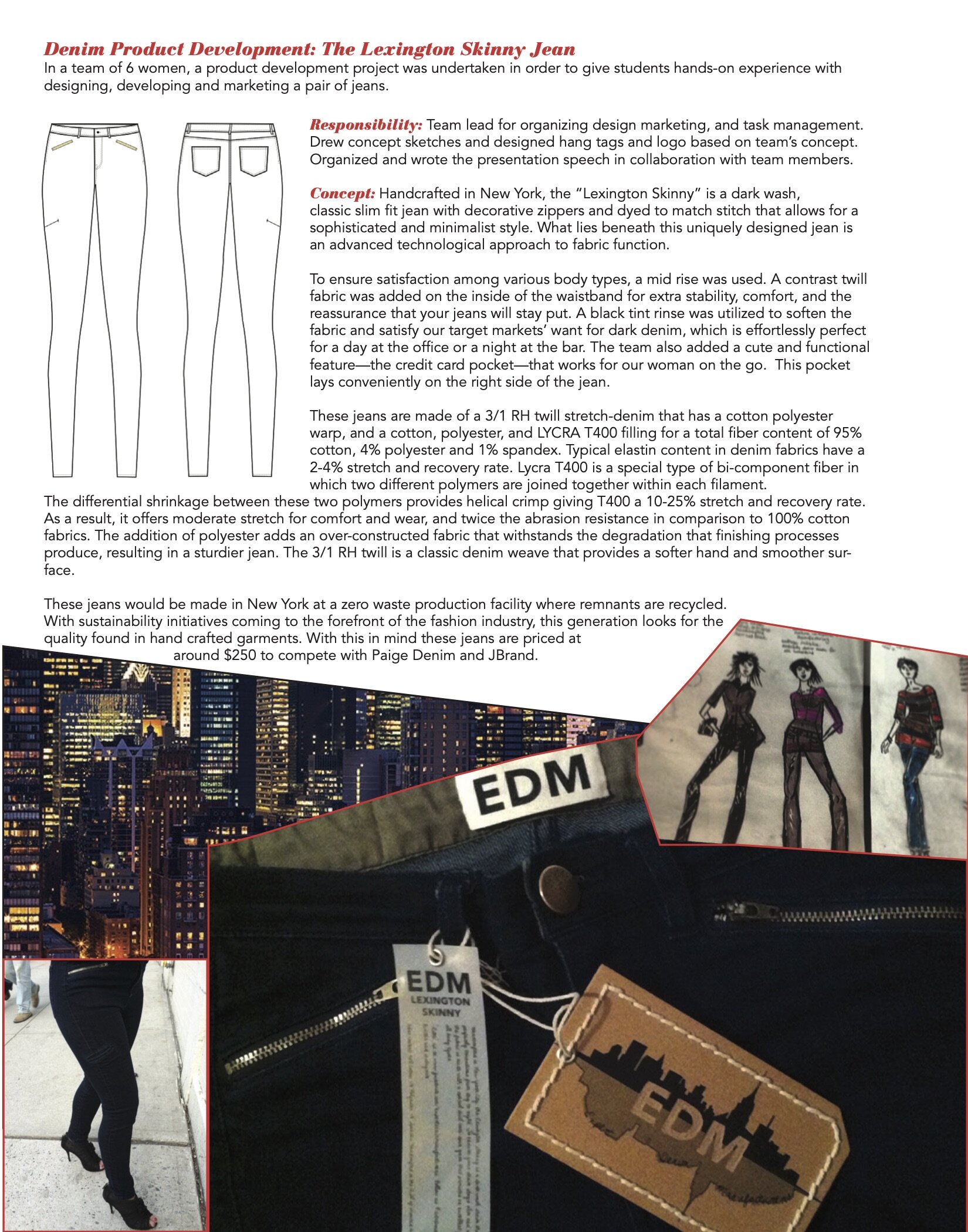
Product development in a group format with other students. Responsibilities included organizing, design, marketing, and task delegation.
Tag designs were exclusively my own.

The goal of this page is to demonstrate an ability to analyze a fabric, and put together a costing card for sourcing or direct manufacturing.
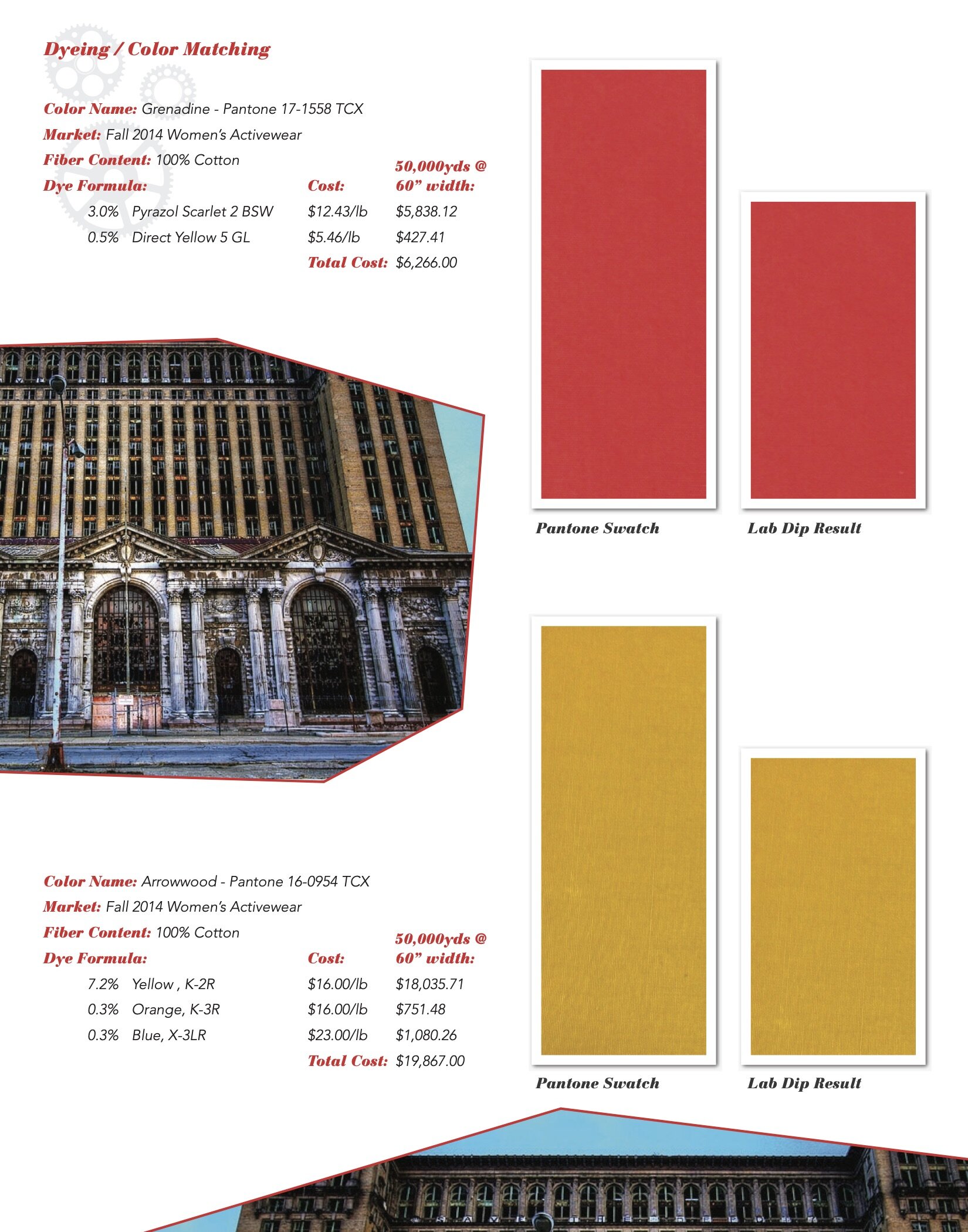
The process of color matching a Pantone swatch started with guessing what dye colors were used and then adjusting lab dip to lab dip until a match was made.
Note: The physical page had the original swatches and lab dip pieces. I scanned each piece individually and did not color correct them.
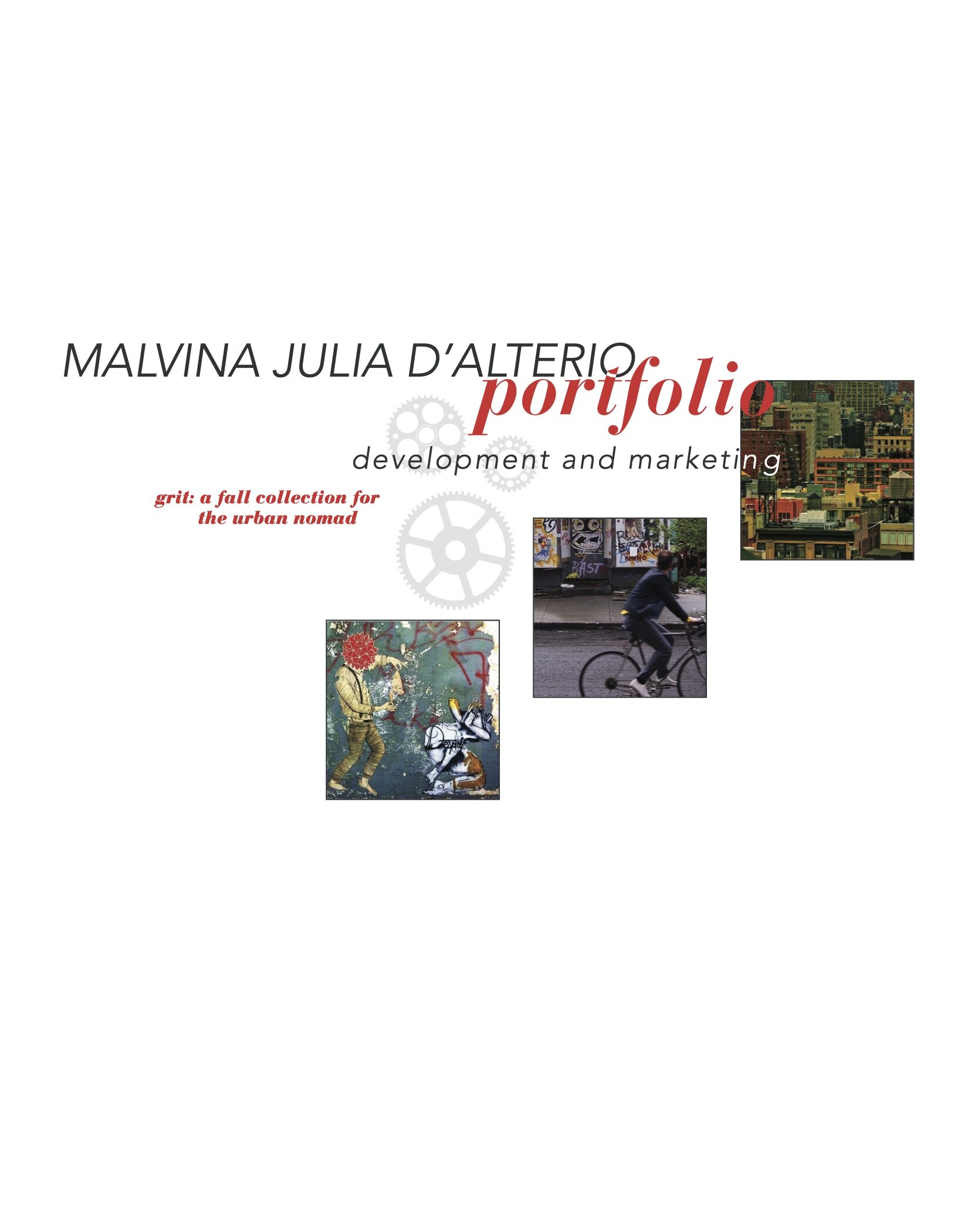
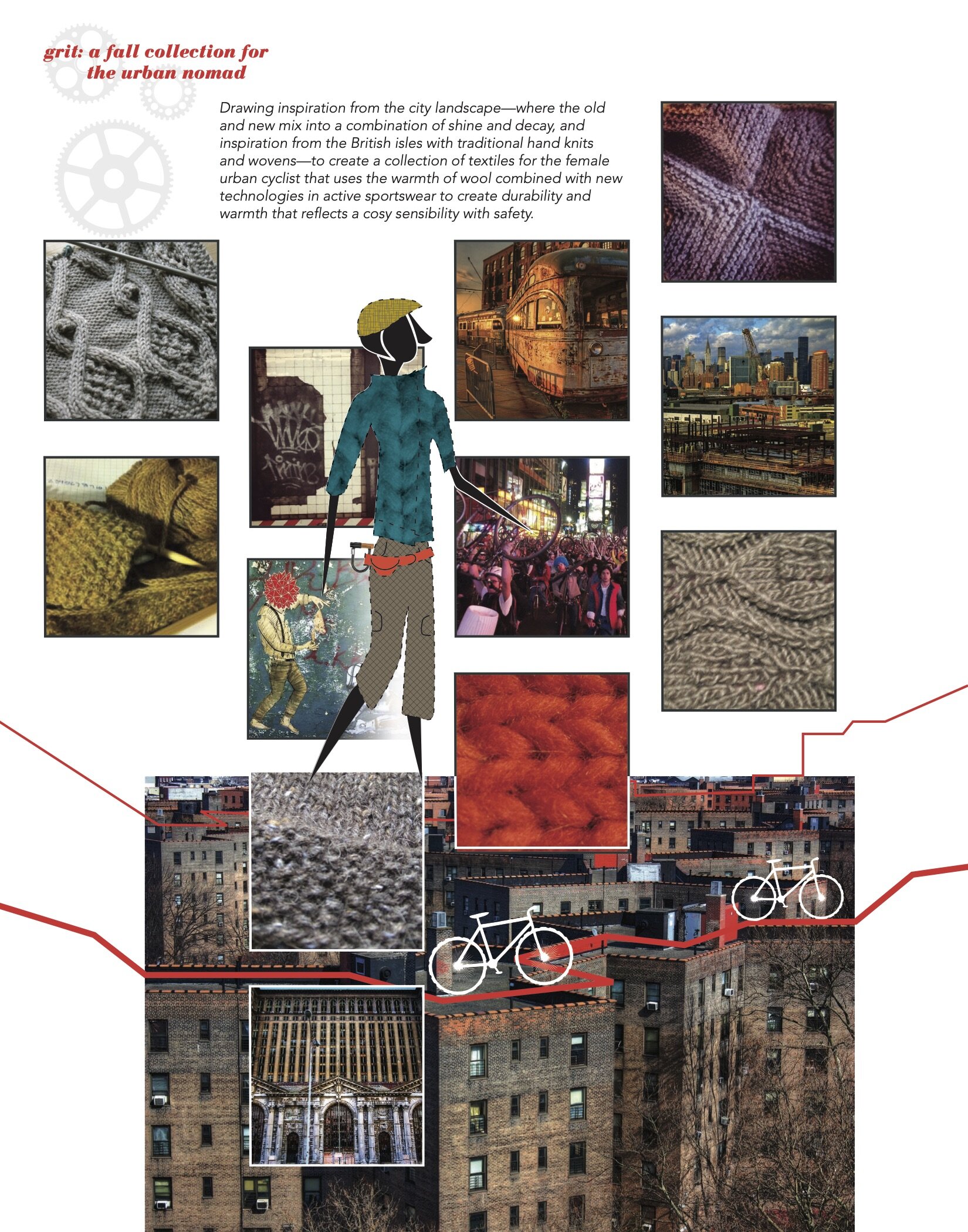
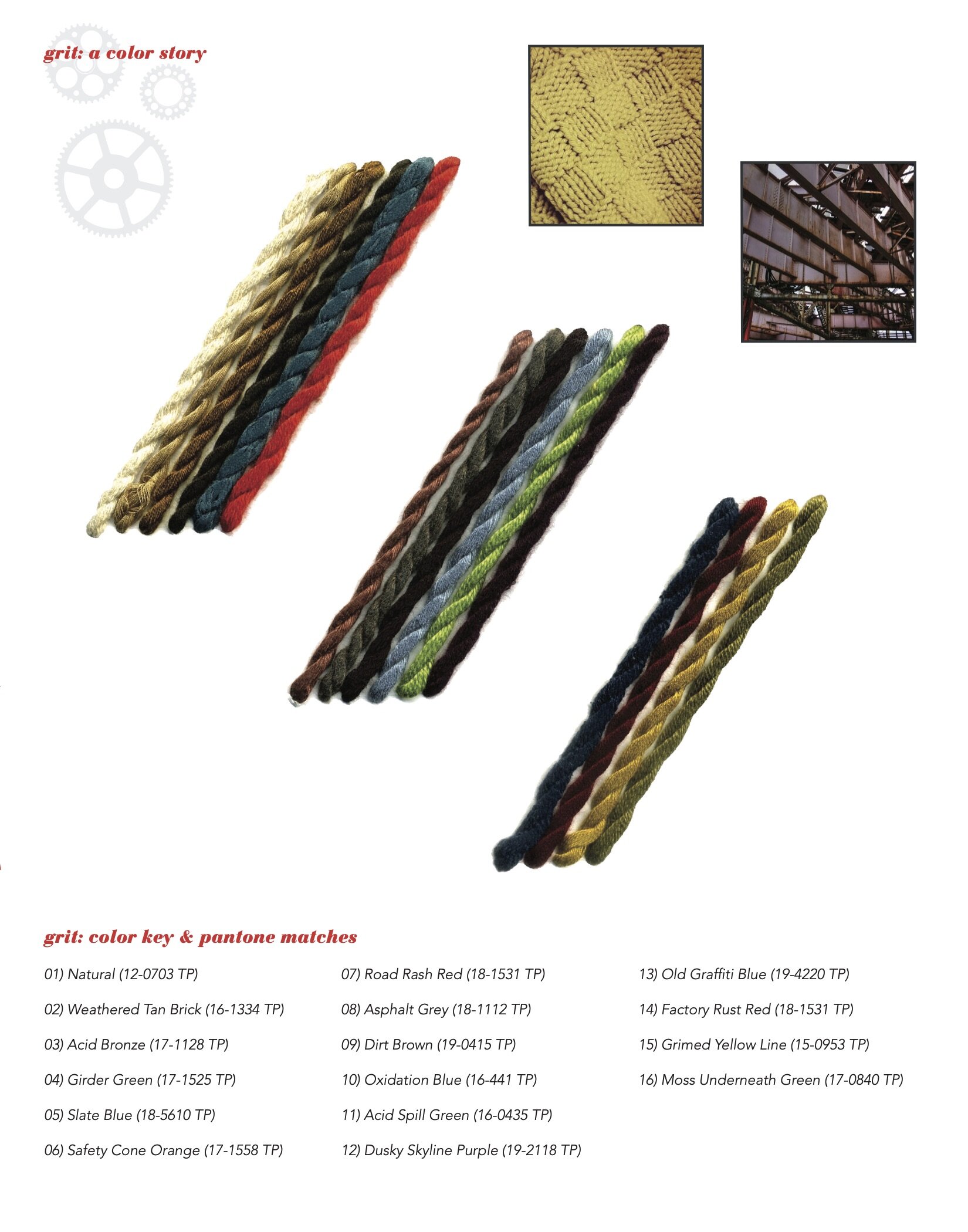
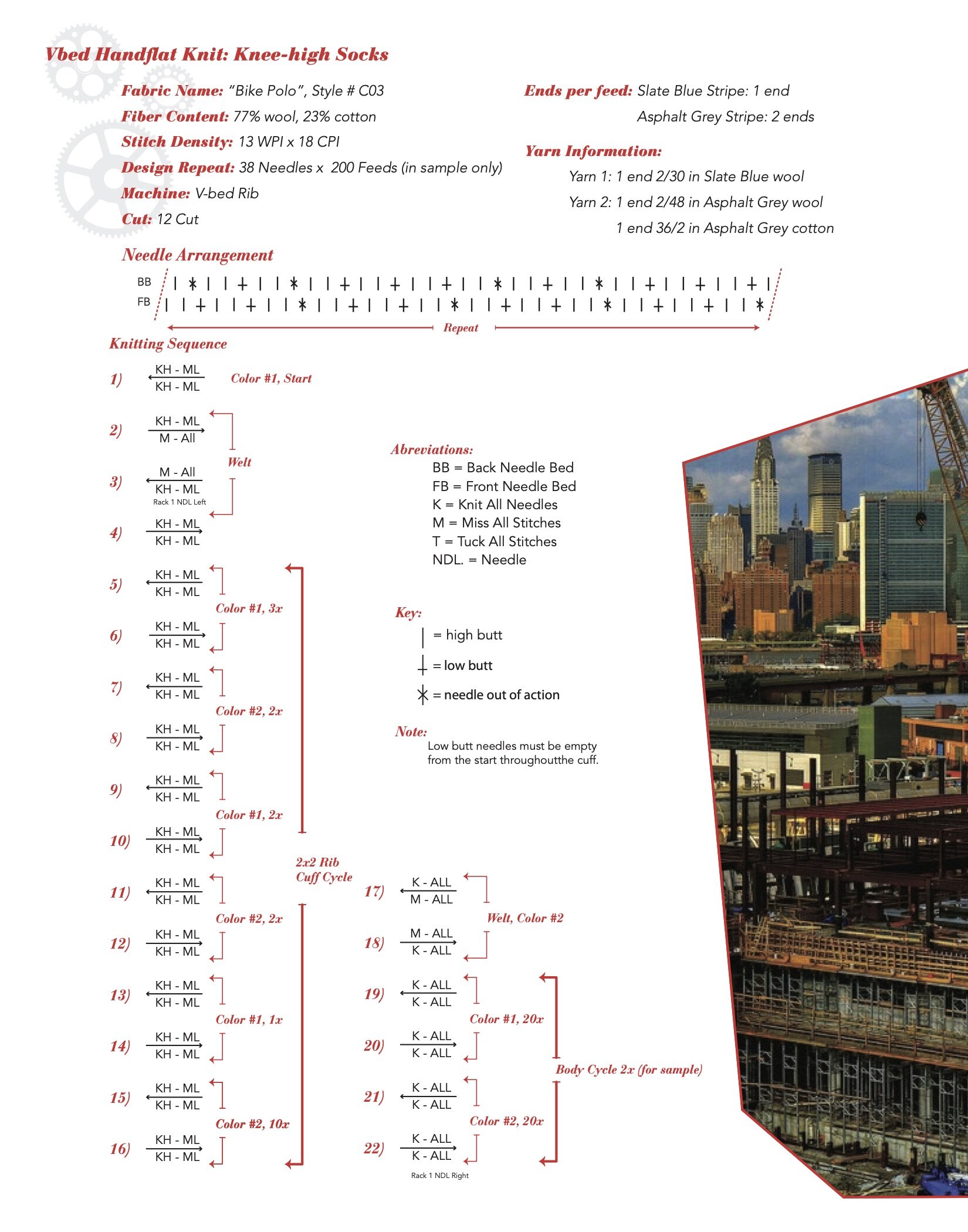

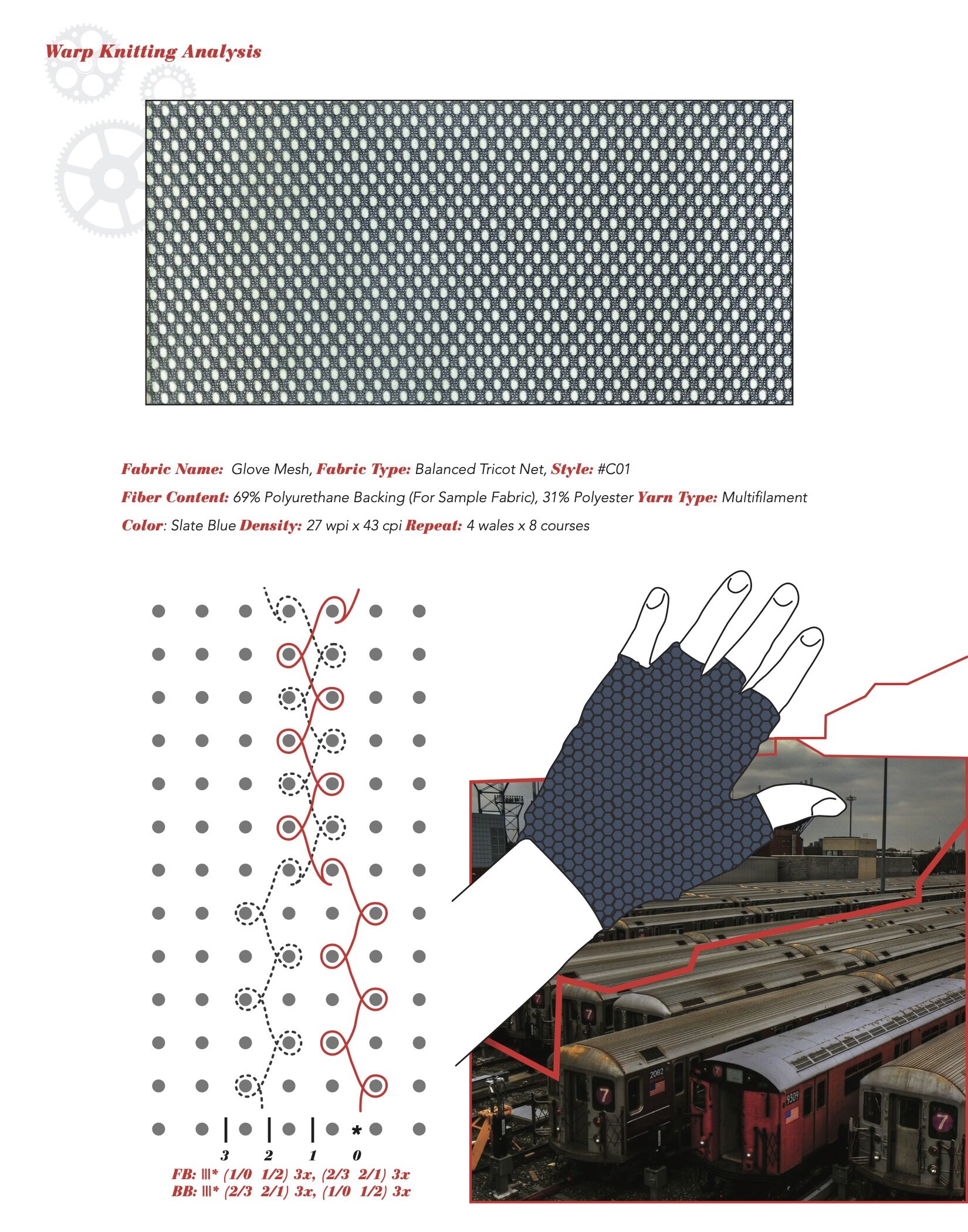
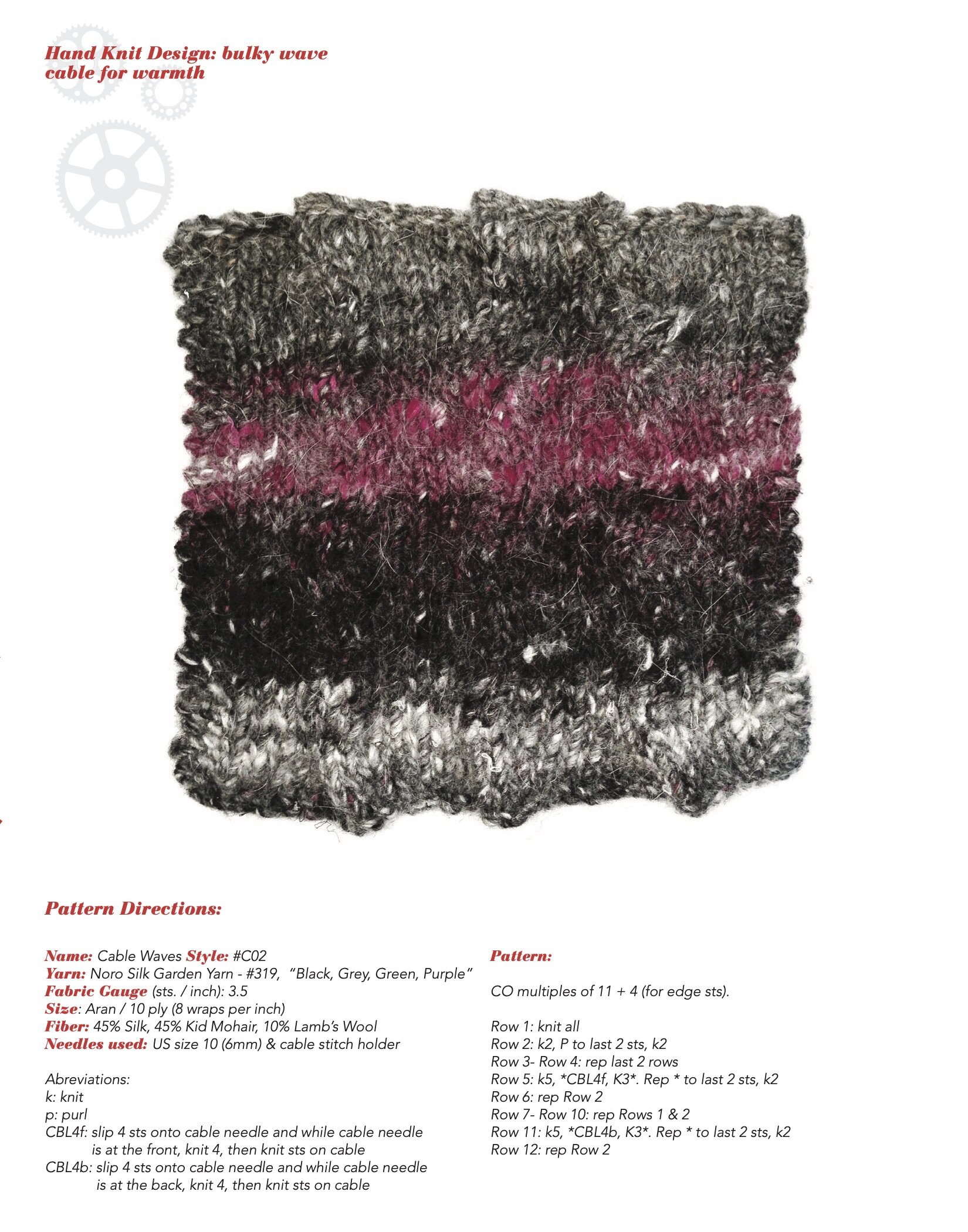
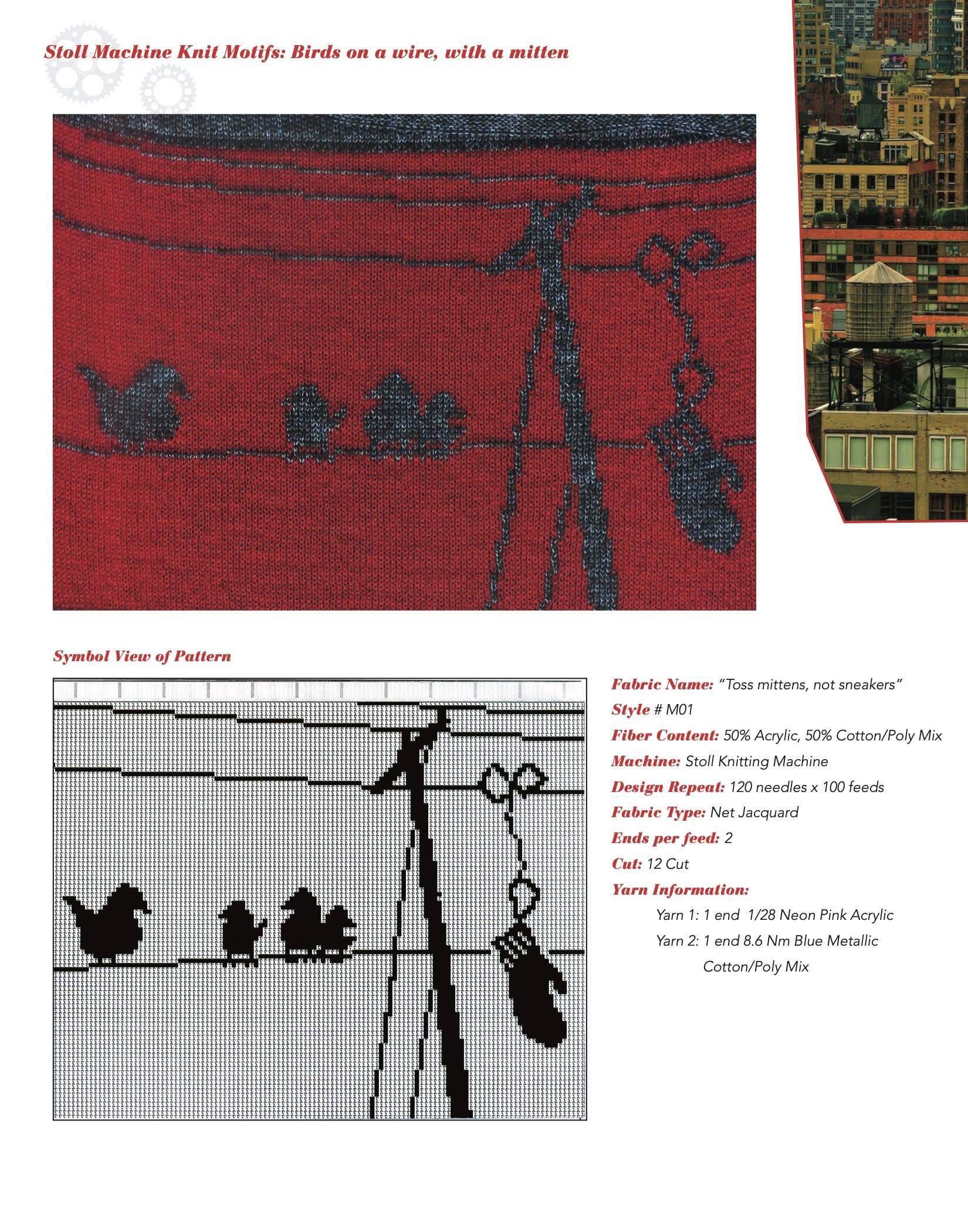
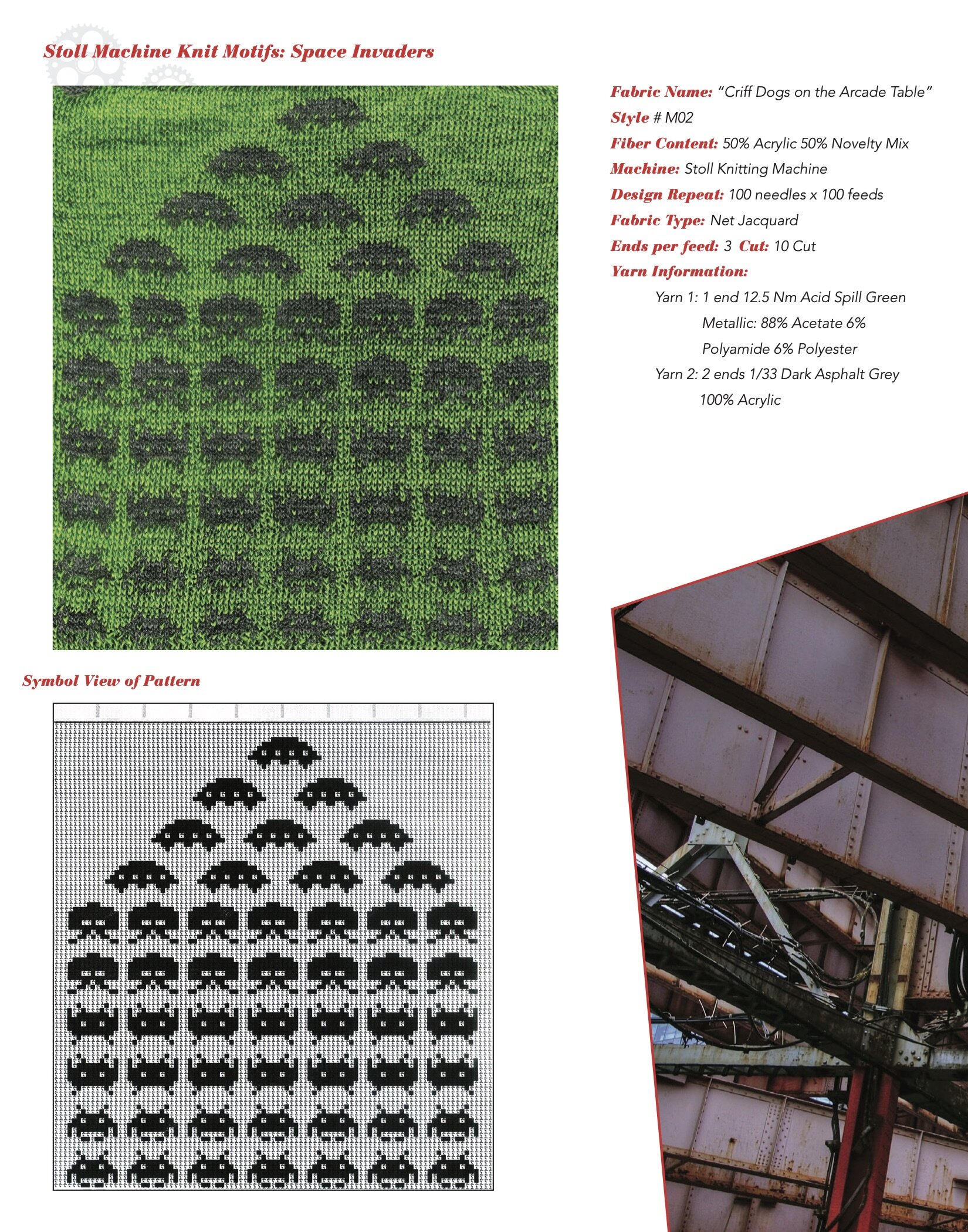
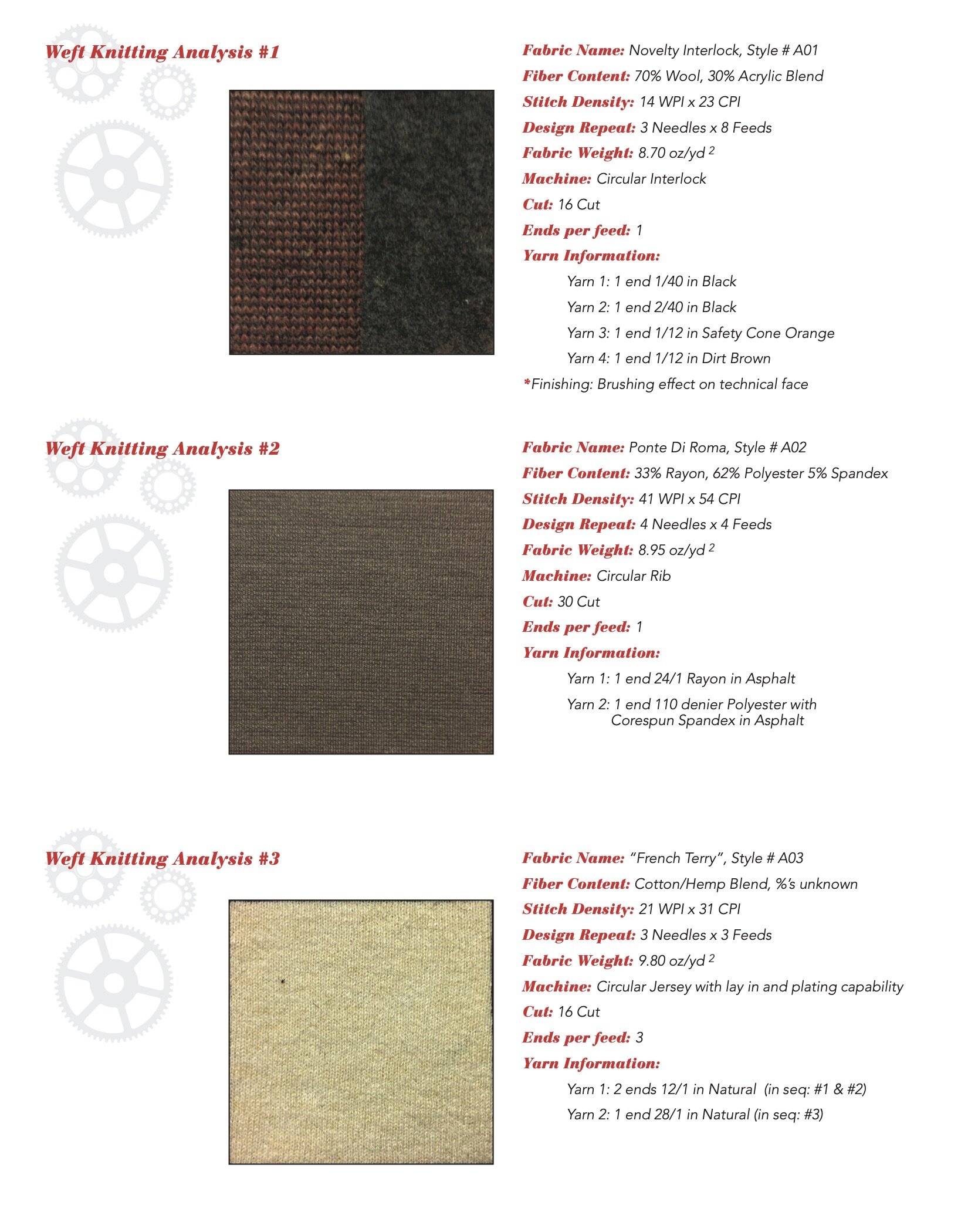
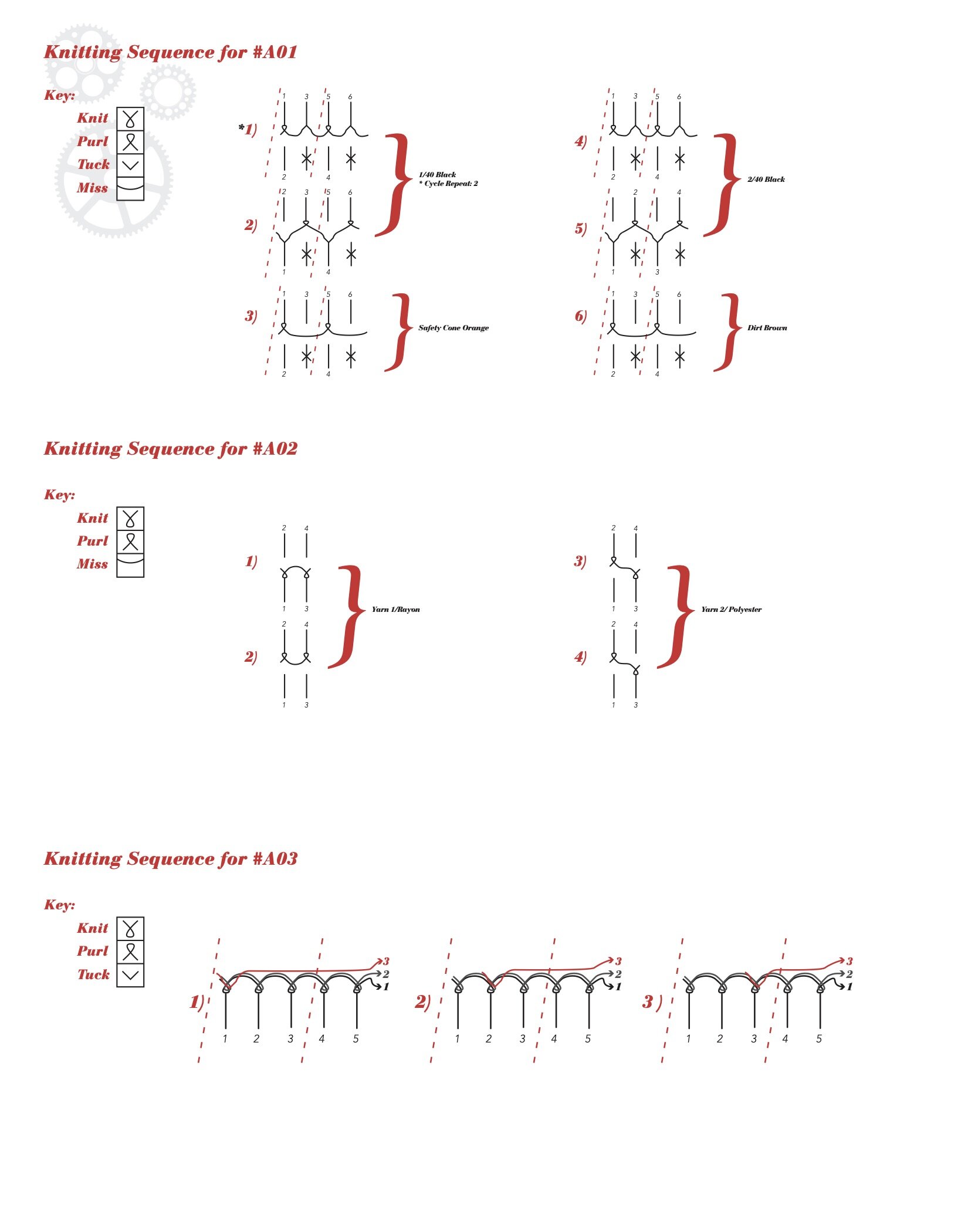
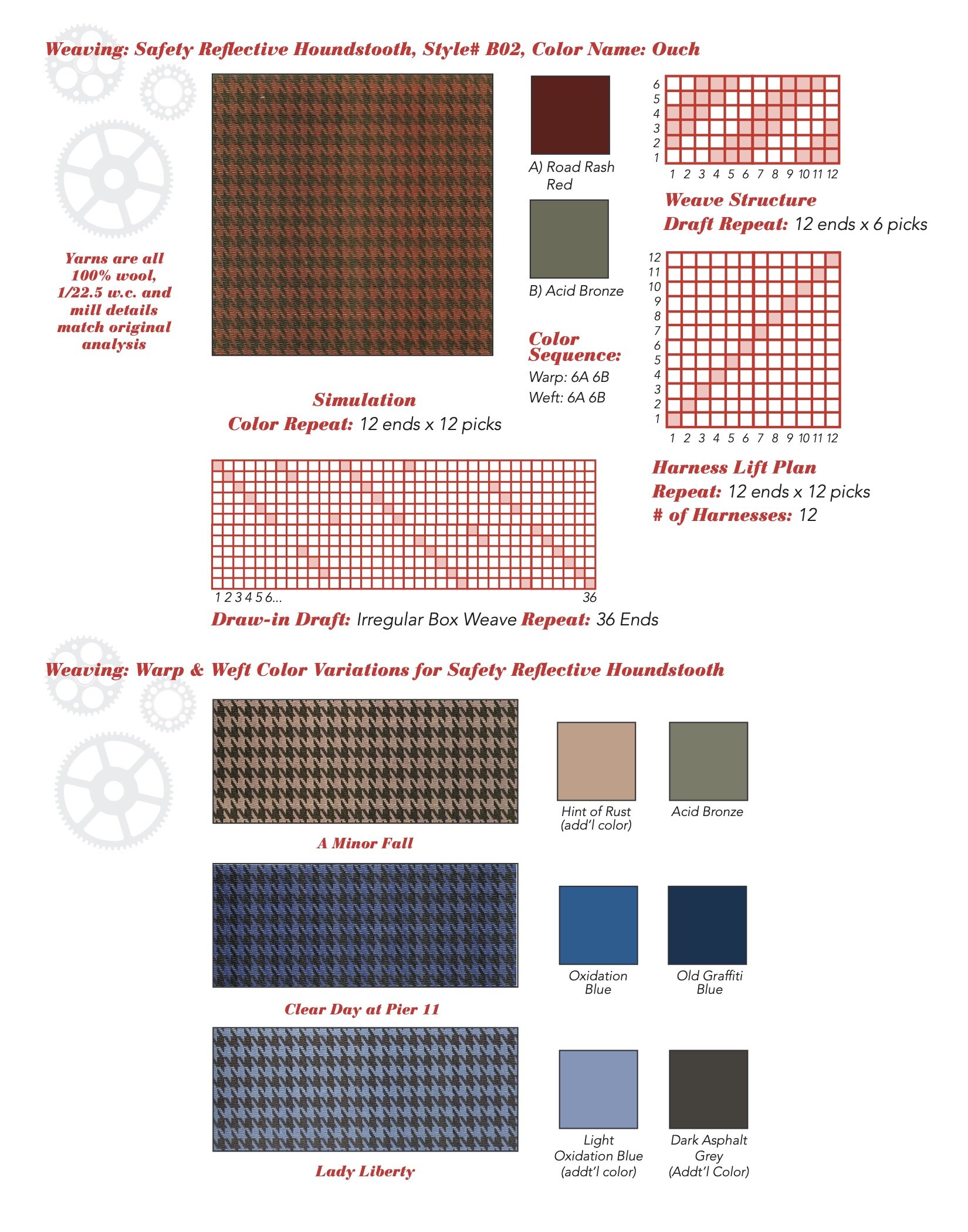
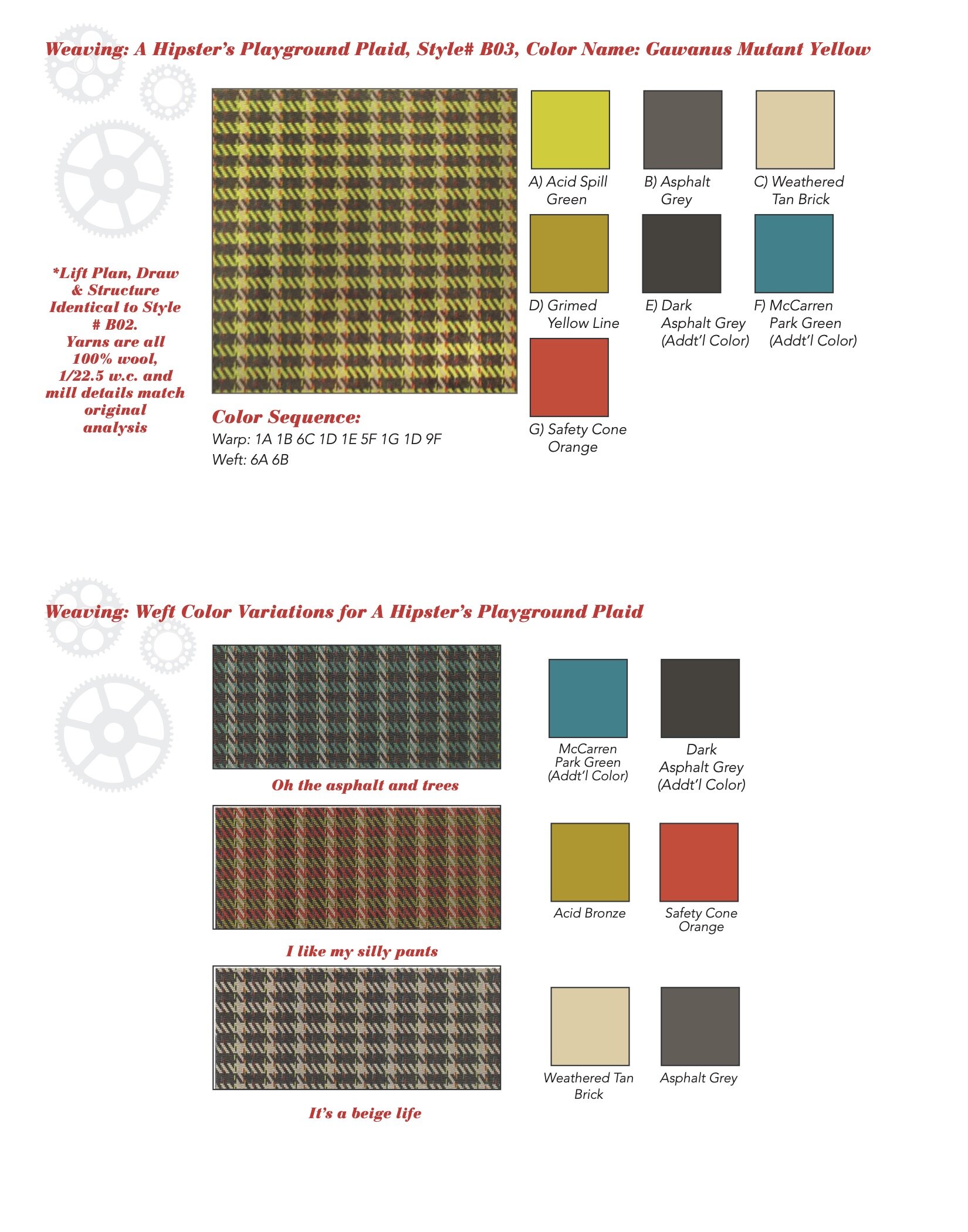
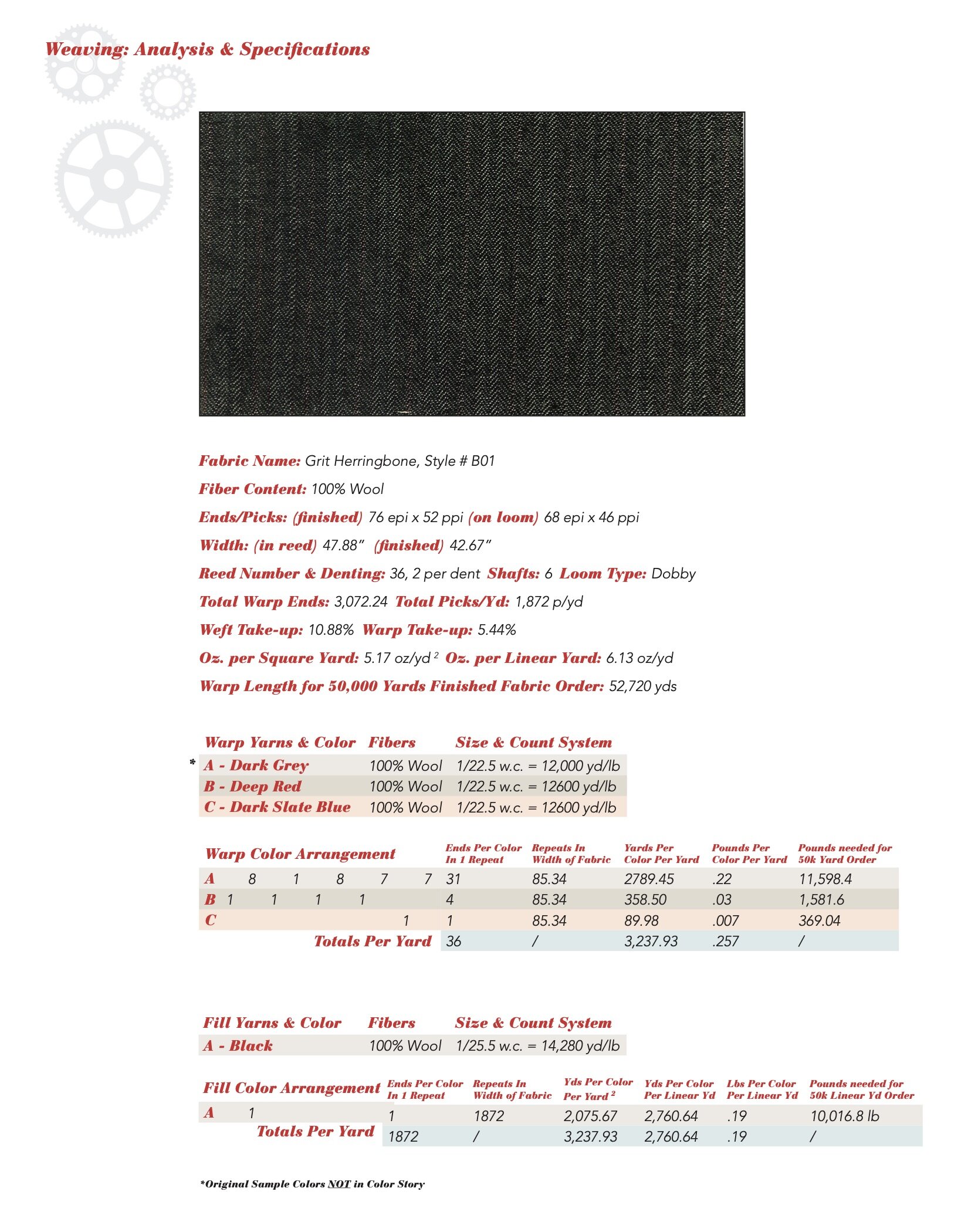
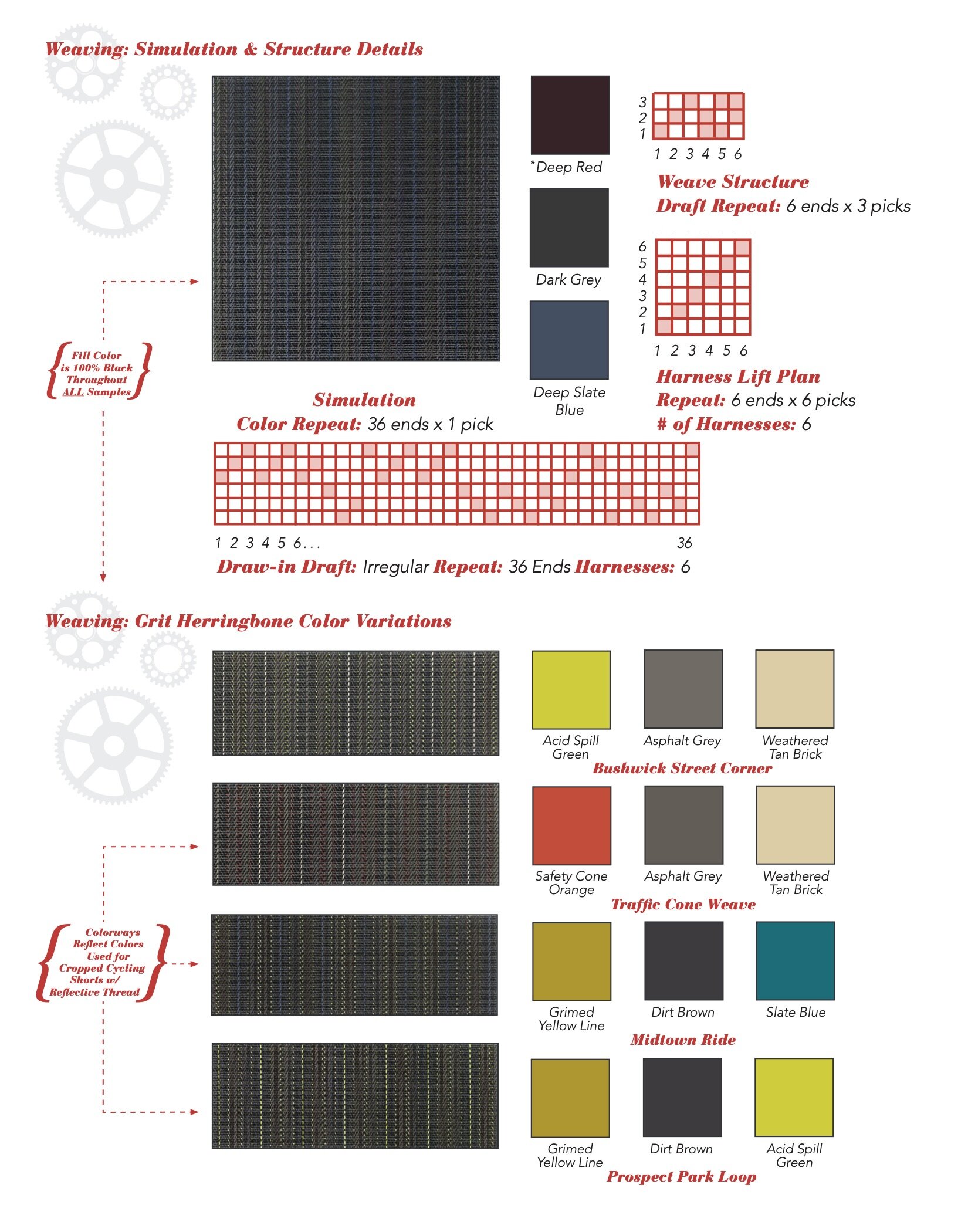
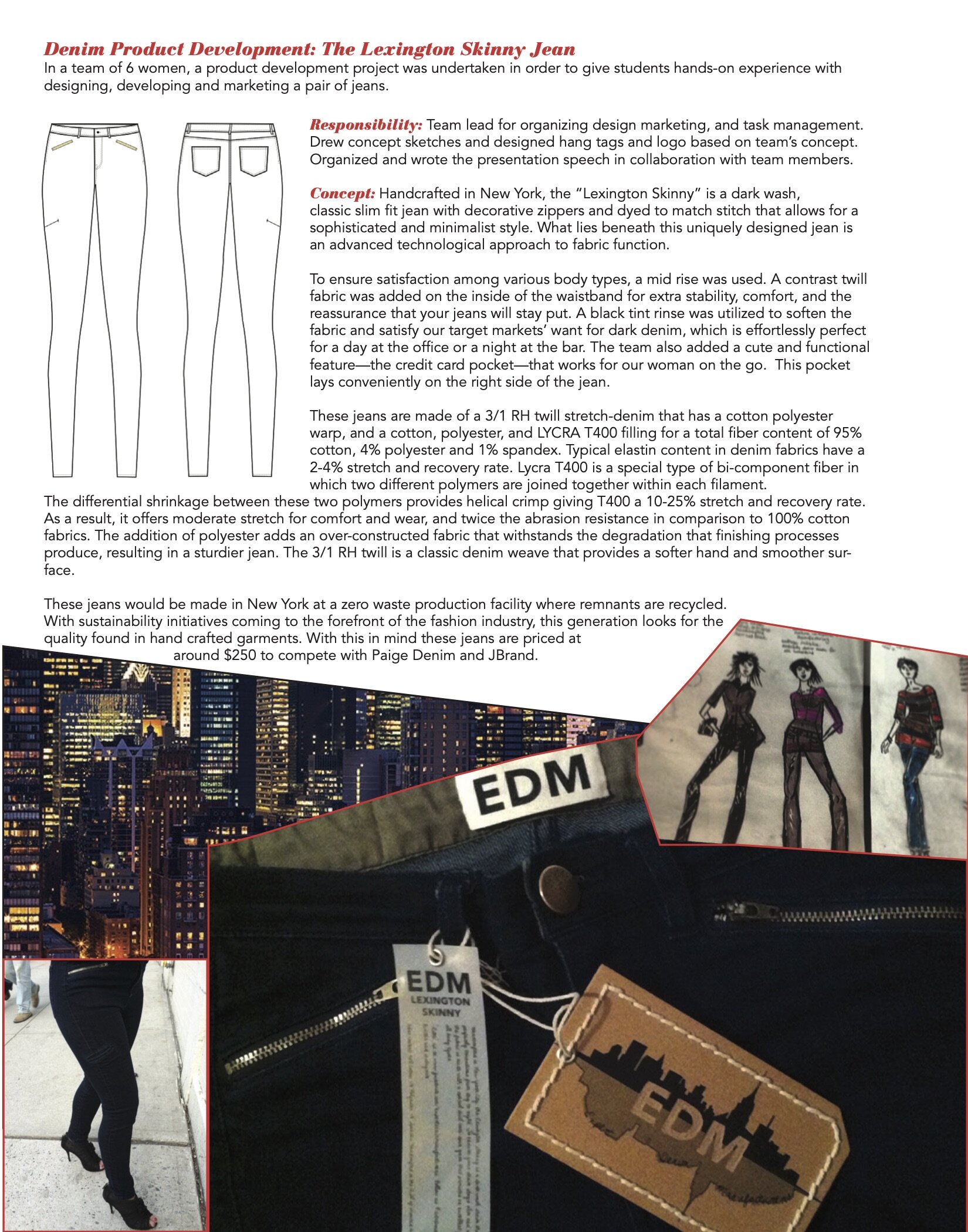

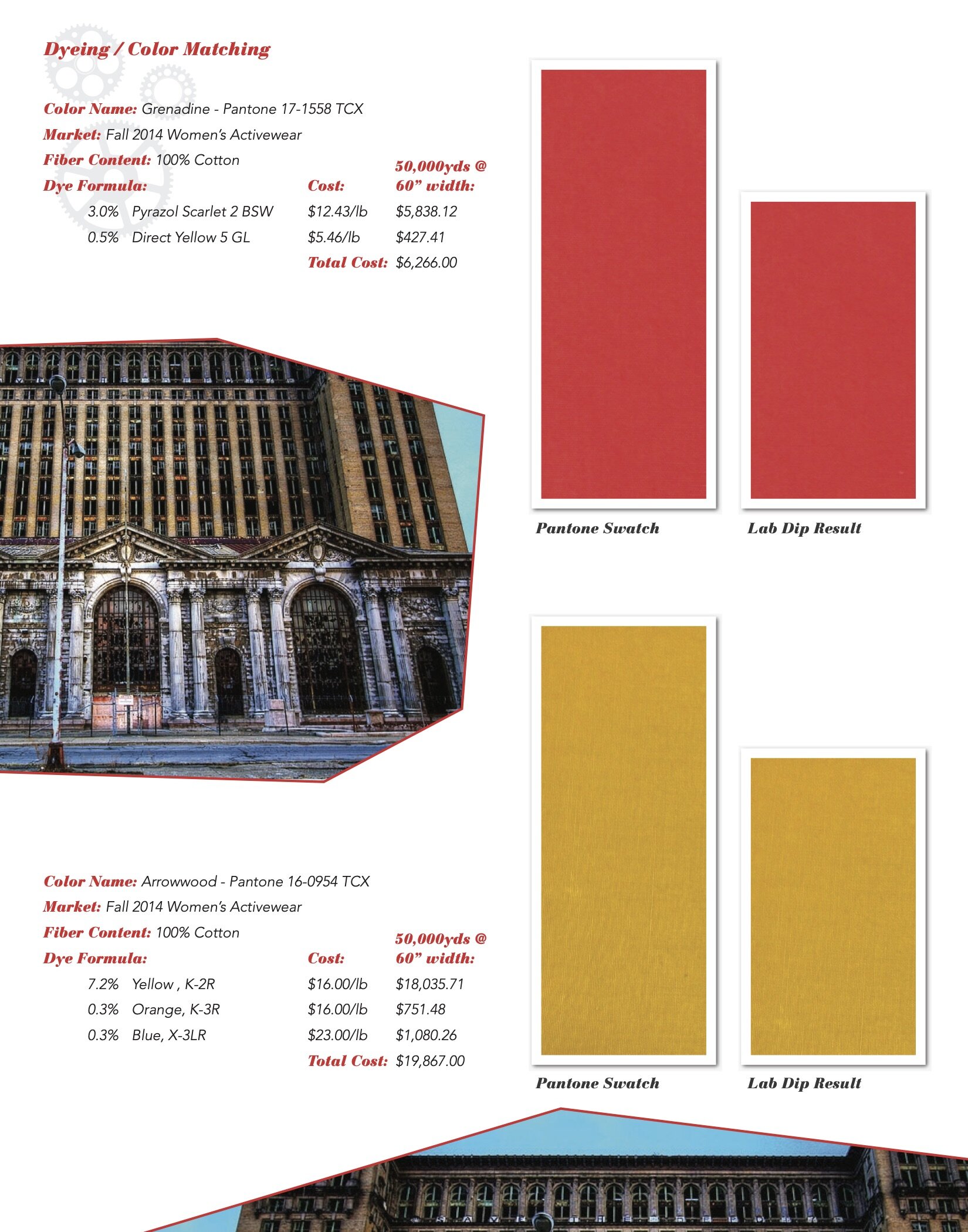
Developed between 2011 - 2014, This is a portfolio of work demonstrating experience developing textiles using both industrial and hand knitting and weaving techniques. The portfolio also includes a capstone project and examples of work done color matching dye and costing fabric for production.
A mood board sets the tone of a project— colors, textures, inspiration, and includes language that briefly explains the project as a whole.
Notes: I fully acknowledge that I used some silly “hipster” terminology for thematic consistency.
Photography Myself or Lucas Cometto (by permission). Locations: Manhattan, Brooklyn, Queens, NY. Detroit, Michigan.
With a mood board, comes a color story.
The portfolio was originally a physical piece of work. Here you can see sets of colored thread, twisted into yarn hanks.
Diagrams and instructions for a Dubied Hand Flat knitting machine. Dubieds are in the shape of an inverted V, allowing for a variety of ribbed and lace-like patterning.
Knitted sample using a v-bed knitting machine, along with the color repeat diagram.
Analysis only, using a standard microscope. Warp knitting machines were not available on the FIT campus for use or demonstration. Warp knitting machines produce generally rigid fabrics, unlike weft knits. These machines are used to make various kinds of mesh and lace-like materials.
This pattern uses cabling techniques without using purl stitches for definition in order to create a wave-like landscape that creates air pockets for additional warmth.
A net jacquard technique using a computer-programmable knitting machine. Software used is called Stoll M1 Plus.
Similar to the first sample in technique, with an oldy but goody pattern.
Weft knitting, or what most people think of as “knitting” is knitting done by hand or machine. All 3 samples are machine-knit. Most (but not all) cut and sew knit garments are made using some kind of circular knitting machine.
Pattern analysis for weft knits using loop diagrams.
This shows the full setup for weaving a houndstooth fabric on a loom. Software used to develop rendering was Easy Weave and Dobby Pro.
Note: There is no need to make a houndstooth this difficult. It can be done on a 4 harness loom. It was only done this way to accommodate the next woven pattern.
I’m pretty sure this pattern was developed first before the houndstooth, and then the houndstooth had to adapt to the number of harnesses required to make this work.
This includes a complete breakdown of an analysis done on a found piece of fabric, including what would be needed to reproduce it on an industrial loom.
Product development in a group format with other students. Responsibilities included organizing, design, marketing, and task delegation.
Tag designs were exclusively my own.
The goal of this page is to demonstrate an ability to analyze a fabric, and put together a costing card for sourcing or direct manufacturing.
The process of color matching a Pantone swatch started with guessing what dye colors were used and then adjusting lab dip to lab dip until a match was made.
Note: The physical page had the original swatches and lab dip pieces. I scanned each piece individually and did not color correct them.